Another day, I just don’t know if I am making the right steps. I made the curved sanding bars and began on the edges. I really didn’t like the pressure/vibration that this method put into the sides. Not using a full external mold, I don’t feel there is enough support.
I found that the sanding “rolled” up hill at the blocks, leaving a peak and that the sanding was uneven. I am not convinced on the curved board method. I did not
Next build I will take the time and effort to construct an external mold.
This afternoon, I glued the kerfing to the back, tomorrow will be the front and then I’ll start on the braces.
Time taken : 3 hours
Tools used : sanding curve, rulers, chisel, pencils, chalk, clamps
AU$'s spent : nil
Wednesday, December 27, 2006
Tuesday, December 26, 2006
Christmas catch up
Today, I found some time away from the christmas toys and food and got down into the shed, listening to the cricket and working on the guitar. I am all over the place at the moment and all over that mistake I made on the end block. My end block was exactly 6mm too short, funny really as my saw has a 3mm wide blade and I made two cuts. I used a couple of pieces of mahogany that I had left over from the OOO to build up the height of the block. As you can see, my end block has slices all the way through it. I am not overly worried really, I have no idea what effect these "fault lines" will have on the final product, I hope none.

I also trimmed my sides. I found that I was not getting the results with a plane so I sharpened up the chisels and that made very light work of getting the sides down. My drama here was after working out the error on the tail block, I didn't trim the neck block. Had to chisel a few millimetres off there.
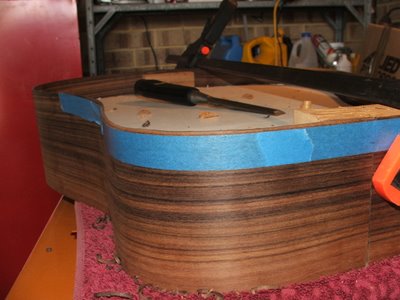
Time taken : 2 hours
Tools used : plane, chisel, sand paper, glue, clamps, rulers, pencils
AU$'s spent : Nil

I also trimmed my sides. I found that I was not getting the results with a plane so I sharpened up the chisels and that made very light work of getting the sides down. My drama here was after working out the error on the tail block, I didn't trim the neck block. Had to chisel a few millimetres off there.
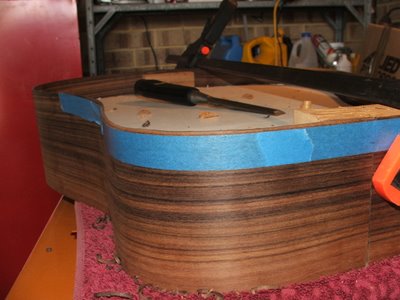
Time taken : 2 hours
Tools used : plane, chisel, sand paper, glue, clamps, rulers, pencils
AU$'s spent : Nil
Wednesday, December 20, 2006
Darn Hurdles
This one was suppose to be easier. Although I am finding the step of brace construction and radiusing the sides quite difficult. am struggling.
During my planning phase, I settled on simply making a “slice” of a sanding dish, as used by Bill Corey, instead of buying a couple of sanding dishes ($US 150.00 + postage). I have tried using wire (metal memory-curled up), extension cord (too heavy), fishing line and string (stretched) all in failed efforts to trace a 30 foot and 15 foot radius to a length of pine.
One of my first efforts seemed to be working out okay – When I finished I had two curves which were basically the same and uneven.
I pulled out the dreadnought cross brace that was included in my Stewmac OOO kit and traced that onto the board and I and happy to use that curve for the top. That leaves just the 15 foot radius.
Anyone got ideas? Any mathematical wizards out there that can work this out? Any one know where I could download a template?
Time taken : a few hours
Tools used : items mentioned above, jigsaw, sand paper, wood file, scraper.
AU$'s spent : $6.00 for the pine
During my planning phase, I settled on simply making a “slice” of a sanding dish, as used by Bill Corey, instead of buying a couple of sanding dishes ($US 150.00 + postage). I have tried using wire (metal memory-curled up), extension cord (too heavy), fishing line and string (stretched) all in failed efforts to trace a 30 foot and 15 foot radius to a length of pine.
One of my first efforts seemed to be working out okay – When I finished I had two curves which were basically the same and uneven.
I pulled out the dreadnought cross brace that was included in my Stewmac OOO kit and traced that onto the board and I and happy to use that curve for the top. That leaves just the 15 foot radius.
Anyone got ideas? Any mathematical wizards out there that can work this out? Any one know where I could download a template?
Time taken : a few hours
Tools used : items mentioned above, jigsaw, sand paper, wood file, scraper.
AU$'s spent : $6.00 for the pine
Sunday, December 17, 2006
My Latest Mistake
Well, I have officially started – and made further mistakes.

I simply used the curved cauls that I made for my Stewmac kit as sanding blocks and curved the face of both the neck block and the end block. The curve is almost exactly the same, certainly a better result than I would have gotten with my eye alone. I knew there was a good reason why I never throw anything away.
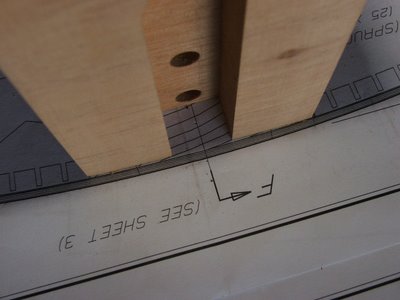
So at the end of the weekend, I get to the point where I want to glue the blocks to the sides. I glued on the neck block and as I was clearing away the glue squeeze out, I noticed that I had left the masking tape on the inside on the edge. Effectively, I had glued the block to the tape and therefore sticky taped my side to the guitar edge. Gotta love bright blue masking tape, if I hadn’t have seen the edge sticky out I might have made it days down the track before I found out. Obviously in the mad rush to pull everything apart again, I don't have time to photograph it.
Anyways, I have glued my blocks on and we're underway again.
Time taken : 3 hours
Tools used : LMI white glue, clamps, sandpaper, pencil, T square, wax paper, rulers
AU$'s spent :

I simply used the curved cauls that I made for my Stewmac kit as sanding blocks and curved the face of both the neck block and the end block. The curve is almost exactly the same, certainly a better result than I would have gotten with my eye alone. I knew there was a good reason why I never throw anything away.
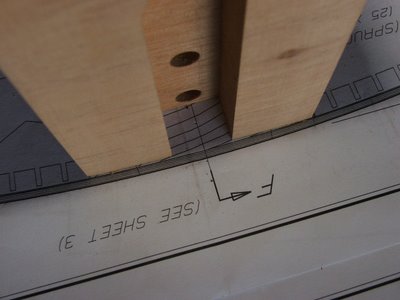
So at the end of the weekend, I get to the point where I want to glue the blocks to the sides. I glued on the neck block and as I was clearing away the glue squeeze out, I noticed that I had left the masking tape on the inside on the edge. Effectively, I had glued the block to the tape and therefore sticky taped my side to the guitar edge. Gotta love bright blue masking tape, if I hadn’t have seen the edge sticky out I might have made it days down the track before I found out. Obviously in the mad rush to pull everything apart again, I don't have time to photograph it.
Anyways, I have glued my blocks on and we're underway again.
Time taken : 3 hours
Tools used : LMI white glue, clamps, sandpaper, pencil, T square, wax paper, rulers
AU$'s spent :
Saturday, December 16, 2006
The first mistake
Well I made my first decent blue today... more on that in a minute.
Since getting the kit, I have bought some foam boards from Office Works and cut out both and internal and external forms, following the LMI dreadnought plan. I have decided to use the StewMac method as I don't think my little Dremel would stand up to all that routing.
So I have a waist clamp in place and I think it will all form something close to the shape that it is suppose to take.
Now, here comes the muck up. LMI do not provide and instruction manual, however they do supply a DVD created by Robert O'Brien in which he makes a LMI OM guitar. So I watch the DVD, I listen and I take note of the steps.
I follow Robert's instruction and cut the end block slightly taller than 100 millimeters. Then I work out that the Dreadnought end block is not to be trimmed to 100... I glued the piece I cut off back on the top. In I would have lost 6 millimeters because I may two cuts and the blade is 3 mill wide.
Time taken :
Tools used :
AU$'s spent :
Since getting the kit, I have bought some foam boards from Office Works and cut out both and internal and external forms, following the LMI dreadnought plan. I have decided to use the StewMac method as I don't think my little Dremel would stand up to all that routing.
So I have a waist clamp in place and I think it will all form something close to the shape that it is suppose to take.
Now, here comes the muck up. LMI do not provide and instruction manual, however they do supply a DVD created by Robert O'Brien in which he makes a LMI OM guitar. So I watch the DVD, I listen and I take note of the steps.
I follow Robert's instruction and cut the end block slightly taller than 100 millimeters. Then I work out that the Dreadnought end block is not to be trimmed to 100... I glued the piece I cut off back on the top. In I would have lost 6 millimeters because I may two cuts and the blade is 3 mill wide.
Time taken :
Tools used :
AU$'s spent :
Monday, December 11, 2006
It's Arrived
It arrived. I am so pleased with the look of the wood however in hindsight, I would not have had a back strip put in as there was what appeared to be a nice light coloured feature in the back as it was. That feature looks kind of muddled up now – still it is beautiful.
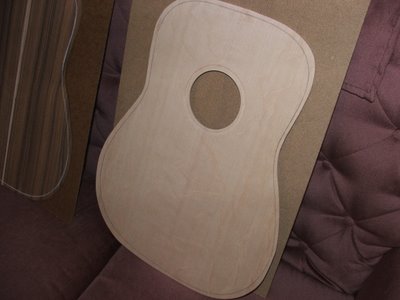

In my opinion, LMI package their kits a lot better than Stew Mac. Tape is used in an attempt to hold the sides in place, each piece is well labeled and securely packaged.
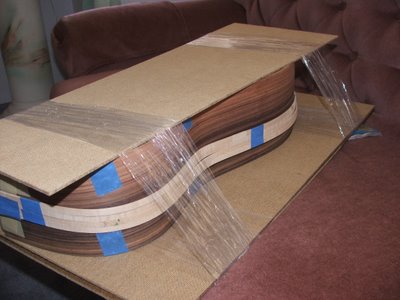
I am also back to square one, worried that I do not have the skills to get this job done. Shaping sides, braces and end blocks worry me. Now I see why everyone recommends that beginners start with a Stew Mac, there are a couple of little fiddly steps that have already been taken care of. Still, I am up for the challenge.
The process begins again.
Time taken :
Tools used :
AU$'s spent :
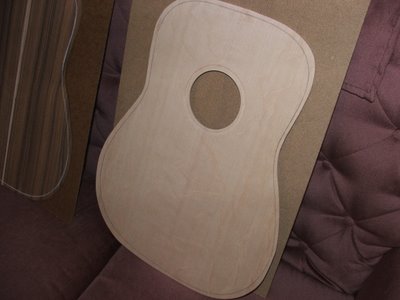

In my opinion, LMI package their kits a lot better than Stew Mac. Tape is used in an attempt to hold the sides in place, each piece is well labeled and securely packaged.
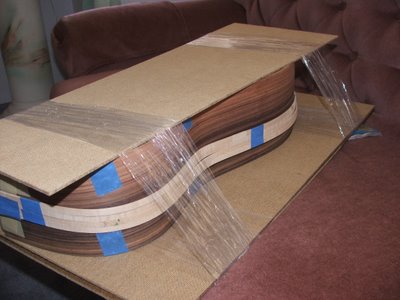
I am also back to square one, worried that I do not have the skills to get this job done. Shaping sides, braces and end blocks worry me. Now I see why everyone recommends that beginners start with a Stew Mac, there are a couple of little fiddly steps that have already been taken care of. Still, I am up for the challenge.
The process begins again.
Time taken :
Tools used :
AU$'s spent :
Sunday, December 10, 2006
It's Not Done Yet
Turned my hand over the weekend to get this action down. It is now lower and near enough to being acceptable, but I do think that I have to one day reset the neck. I am a couple of millimeters out here and there but it all adds up. I think next time I will set the neck before the fingerboard goes on.
The finish - I just don't know about. I don't yet know if the KTM-9 handles sweat well. There is an obvious haze where my strumming arm rests on the body. I wash often (honest). Also, I don't think that my Martin Guitar Co. cleaner suits the KTM-9. Perhaps the Martin product is suited to a Nitro styled finish... might keep testing and see what results I get over time.
I was in the guitar shop the other day and really liked the raw Martins and Matons, with no finish, no bindings - raw. Might have already planned number three.... ooopss
Time taken : 1 hour or so
Tools used : vice, file, string winder
AU$'s spent : Nil
The finish - I just don't know about. I don't yet know if the KTM-9 handles sweat well. There is an obvious haze where my strumming arm rests on the body. I wash often (honest). Also, I don't think that my Martin Guitar Co. cleaner suits the KTM-9. Perhaps the Martin product is suited to a Nitro styled finish... might keep testing and see what results I get over time.
I was in the guitar shop the other day and really liked the raw Martins and Matons, with no finish, no bindings - raw. Might have already planned number three.... ooopss
Time taken : 1 hour or so
Tools used : vice, file, string winder
AU$'s spent : Nil
Friday, December 08, 2006
It's on its way
Fedex have sent me an Email, letting me know that my new kit is on its way. I can't wait. I think I am just as excited as I waqs with the first one. I ordered the kit on the 27th of November so it only took LMI about 10 days to gather the material and service the parts that I needed. Obviously they couldn't just grab the box off the shelf like a prepared kit from Stewart-Macdonald
Friday, December 01, 2006
Things are getting better.
The OOO is really starting to settle. More likely, I am getting used to playing the wider neck. I still have some adjusting to do and I need to glue in a piece of card or what not.
It appears that LMI have not yet sent my new kit. Somewhat my fault because I threw in a glue order at the last moment. I guess LMI also have to individually pack the pieces of the kit so it'll take more time than just grabbing a box off the shelve.
I am also now in panic mode that the maple binding will not match or suit the Pau Ferro back and sides. It is have to visualise what woods will actually look like at when put together.
It appears that LMI have not yet sent my new kit. Somewhat my fault because I threw in a glue order at the last moment. I guess LMI also have to individually pack the pieces of the kit so it'll take more time than just grabbing a box off the shelve.
I am also now in panic mode that the maple binding will not match or suit the Pau Ferro back and sides. It is have to visualise what woods will actually look like at when put together.
Tuesday, November 28, 2006
Here we go again.
I have all but finished the OOO. I've let it settle and slowly worked the saddle down, getting close to an acceptable action height.
The big news is that I have ordered my second kit, basically the drednought that I worked up on the LMI Kit Wizard. The plan is that by the time it arrives in the post, settles to my climate etc, I will have the OOO complete.
Still before I get too far ahead of myself, here are some photos I took yesterday. Warts and all, I haven't polished the guitar or worked the angles and lighting to have you belive I have a fantastic finish.



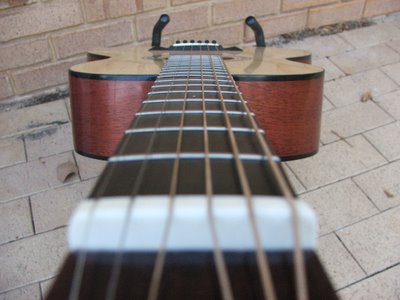
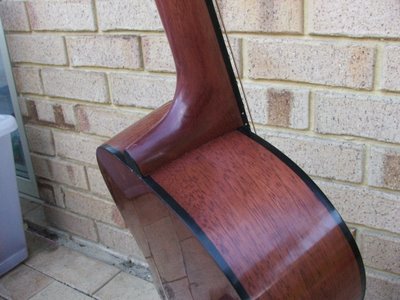
One day soon I will redo the finish on the headstock - it just doesn't rate in my list of priorities at the moment - Playing the guitar does.
The big news is that I have ordered my second kit, basically the drednought that I worked up on the LMI Kit Wizard. The plan is that by the time it arrives in the post, settles to my climate etc, I will have the OOO complete.
Still before I get too far ahead of myself, here are some photos I took yesterday. Warts and all, I haven't polished the guitar or worked the angles and lighting to have you belive I have a fantastic finish.



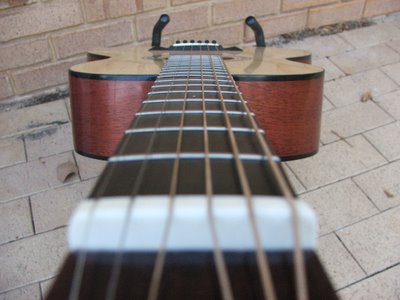
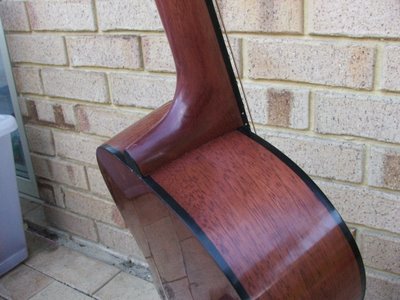
One day soon I will redo the finish on the headstock - it just doesn't rate in my list of priorities at the moment - Playing the guitar does.
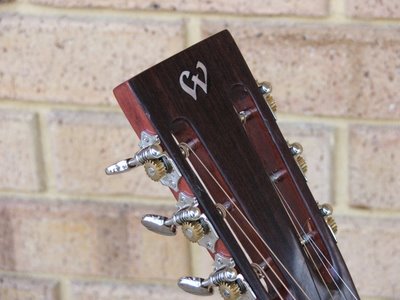
Wednesday, November 22, 2006
Reflection
Okay, so here is the rough enough answers. I had a count back and can tell you that I spent AUD $1,387.45 building this guitar. I still don’t know if I consider that to be extreme. Had I not been able to gain access to a lot of my father’s tools, this would have been a whole lot more. Then again, on the flip side, I bought a lot of new tools, expenses that I will not have to spend on the next guitar
From adding up the blog entries, I have spent 112 days and 89 hours on the construction the guitar so far. Rounding up and down I would say that it will take the average hack (like me) about 100 hours to complete their first guitar.
Food for thought.
From adding up the blog entries, I have spent 112 days and 89 hours on the construction the guitar so far. Rounding up and down I would say that it will take the average hack (like me) about 100 hours to complete their first guitar.
Food for thought.
Tuesday, November 21, 2006
The dust is starting to settle
Okay so I got home today and worked out that my enthusiasm late last night was not really that warranted. I am still very happy but I still have a little way to go to get the instrument to settle.
My rant about the action being acceptable was purely a lie, it is not. The guitar is playable but still a long way away from being pleasurable. Not bad at the nut end but way too high at the saddle. Still that won't be too hard to fix up.
I have not touched the truss road yet and I have some reading on that subject to do. I have roughly sawed in the grooves into the nut and I have a nice distance between the strings.
Still, when all is said and done - I built a guitar.
Time taken : 1 hour
Tools used : saw, pencil, string winder
AU$'s spent : Nil
My rant about the action being acceptable was purely a lie, it is not. The guitar is playable but still a long way away from being pleasurable. Not bad at the nut end but way too high at the saddle. Still that won't be too hard to fix up.
I have not touched the truss road yet and I have some reading on that subject to do. I have roughly sawed in the grooves into the nut and I have a nice distance between the strings.
Still, when all is said and done - I built a guitar.
Time taken : 1 hour
Tools used : saw, pencil, string winder
AU$'s spent : Nil
Monday, November 20, 2006
It's a guitar
I've done it. I've played it. I've heard it. I am happy.
I've been flying tonight. I got home from work and took the clamps of the bridge, I drilled the bridge pin holes and then used a tapered file to seat the pins.
Then I roughed out the saddle and put on the E strings... and then I put on the other four strings... threw a capo on the second fret and roughed out the spaces between the strings.... tuned it up about 3/4 pitch and started to play.

I love it. It sounds just as good as my Yamaha right now. The action is just as good as my Yamaha right now. I am amazed how simple it was to play even through the strings were sitting on rough height saddles and nut.

Somehow I need to get to sleep. I would play all night but I sanded off the end of my fingers whilst rubbing down the saddle.
Time taken : 3 hours
Tools used : clamps, drill, sandpaper, clamps, vice, rulers, files, pencil.
AU$'s spent : $9.95 set of strings
I've been flying tonight. I got home from work and took the clamps of the bridge, I drilled the bridge pin holes and then used a tapered file to seat the pins.
Then I roughed out the saddle and put on the E strings... and then I put on the other four strings... threw a capo on the second fret and roughed out the spaces between the strings.... tuned it up about 3/4 pitch and started to play.

I love it. It sounds just as good as my Yamaha right now. The action is just as good as my Yamaha right now. I am amazed how simple it was to play even through the strings were sitting on rough height saddles and nut.

Somehow I need to get to sleep. I would play all night but I sanded off the end of my fingers whilst rubbing down the saddle.
Time taken : 3 hours
Tools used : clamps, drill, sandpaper, clamps, vice, rulers, files, pencil.
AU$'s spent : $9.95 set of strings
Sunday, November 19, 2006
Mixed Emotions
Today I did the sanding and polishing of the neck, added on the tuning machines and fitted the bridge.
For some reason, and I have no idea why, the KTM-9 blistered on the headstock. The finish is useless in one small spot. It is a cosmetic issue really but you can see it easily and it sucks up the "wow factor" when you look at the guitar. I think I can spot fix it later but I am going to push forward for now. I need to hear this guitar.
I stripped back the finish on the soundboard and glue on the bridge. The process was a little daunting but I think that I have it in the right position without too much trouble at all.
Time taken : 2 hours
Tools used : sand paper, polish, drill, buffer, rules tape, paint stripper.
AU$'s spent : Nil
For some reason, and I have no idea why, the KTM-9 blistered on the headstock. The finish is useless in one small spot. It is a cosmetic issue really but you can see it easily and it sucks up the "wow factor" when you look at the guitar. I think I can spot fix it later but I am going to push forward for now. I need to hear this guitar.
I stripped back the finish on the soundboard and glue on the bridge. The process was a little daunting but I think that I have it in the right position without too much trouble at all.
Time taken : 2 hours
Tools used : sand paper, polish, drill, buffer, rules tape, paint stripper.
AU$'s spent : Nil
Thursday, November 16, 2006
Off comes the masking tape
Tired of waiting. I've had the neck out in the sunlight (warmth) a fair bit and all looked hard so I took the masking tape off the fretboard tonight. Not exactly disappointed but I am sure I could have achieved better results with a better technique.
My only problem is establishing the angle were the finish ends and the fretboard surface starts.
I tried using a sanding block to rub back the edge of the masking tape but the fret edges were causing difficulties. I ended up sliding a razor blade along the fretboard surface. The final product is not that bad however I can really see were the masking tape fell lower than the fretboard even though it was only a couple of millimeters here and there.
Before I try that again, I will be seeking ideas how people mask, and more importantly, remove the masking tape.
Time taken : I hour
Tools used : scalpel
AU$'s spent : Nil
My only problem is establishing the angle were the finish ends and the fretboard surface starts.
I tried using a sanding block to rub back the edge of the masking tape but the fret edges were causing difficulties. I ended up sliding a razor blade along the fretboard surface. The final product is not that bad however I can really see were the masking tape fell lower than the fretboard even though it was only a couple of millimeters here and there.
Before I try that again, I will be seeking ideas how people mask, and more importantly, remove the masking tape.
Time taken : I hour
Tools used : scalpel
AU$'s spent : Nil
Wednesday, November 15, 2006
Tick Tock, Tick Tock
I am tired of waiting for the KTM-9 to dry. I wanna keep going.
On Sunday I went down to Bunnings and explained to a staff member my needs in making a caul or three in order to clamp (and drill) the bridge into place. I was suggested to try Selleys Knead It. The product is basically a putty that you work in your hand, making it softer as you go, it will then from to any shape you want. Once left to set, it sets rock hard.

So, I protected the bridge with plastic wrap and went to work, making three cauls. I am impressed with the results. Clean and very hard
Time taken : 30 minutes
Tools used : Selleys Knead It
AU$'s spent : $14.95
On Sunday I went down to Bunnings and explained to a staff member my needs in making a caul or three in order to clamp (and drill) the bridge into place. I was suggested to try Selleys Knead It. The product is basically a putty that you work in your hand, making it softer as you go, it will then from to any shape you want. Once left to set, it sets rock hard.

So, I protected the bridge with plastic wrap and went to work, making three cauls. I am impressed with the results. Clean and very hard
Time taken : 30 minutes
Tools used : Selleys Knead It
AU$'s spent : $14.95
Thursday, November 09, 2006
Still fence sitting
I just can't commit. There is no doubt that I want to make a dreadnaught next but after playing around with the LMI Kit Wizard, the end price (for what I want) is AUD$722.53... and that isn't really an "all the fruit" package.
Now compare that with the StewMac Mahogany Dreadnaught at AUD$467.21 (plus cost of tuners)
Should I have another practive or just start making what I want and hope that I forget about the AUD$255.32 difference?
Is 3/4 of a thousand dollars too much to pay for a hobby? I have December off work and wanted to have the wood acclimatised and ready to go by then.
Time taken :
Tools used :
AU$'s spent :
Now compare that with the StewMac Mahogany Dreadnaught at AUD$467.21 (plus cost of tuners)
Should I have another practive or just start making what I want and hope that I forget about the AUD$255.32 difference?
Is 3/4 of a thousand dollars too much to pay for a hobby? I have December off work and wanted to have the wood acclimatised and ready to go by then.
Time taken :
Tools used :
AU$'s spent :
Sunday, November 05, 2006
What am I doing?
Should I be researching my next guitar before I have even finished this one? I haven't picked up a guitar (to play) in about 100 days, what would I do with another one? What am I going to do with myself over the next couple of weeks, whilst I wait for the finish to cure... I could have started on my next one...
What if this one turns out sounding like an elastic band stretched over a wet cardboard box?
Do I really need to spend all that money of building something flash or should I just try another basic kit.
What if this one turns out sounding like an elastic band stretched over a wet cardboard box?
Do I really need to spend all that money of building something flash or should I just try another basic kit.
Planning - Phase II
LMI's Kit Wizard has become my own little dream factory. I've changed a dozen things a thousand times. Hours of unproductive fun. I wish they had more pictures of the woods and bindings etc, a true novice like myself can not picture the final product.
This is what I am leaning towards at the moment... Either that or a straight out Drednought kit from StewMac.

Click on the picutre and then expand - so you can read it.
What are your thoughts? Have I forgotten anything (other than the trus rod)?
This is what I am leaning towards at the moment... Either that or a straight out Drednought kit from StewMac.

Click on the picutre and then expand - so you can read it.
What are your thoughts? Have I forgotten anything (other than the trus rod)?
Saturday, November 04, 2006
Photos as requested
Keeping in mind that I have not rubbed back and polished the neck at all, and the body needs a little more attention. This is the way she is looking at this time.


I am itching to keep going but I NOW think there is merit in letting KTM-9 harden over the following weeks... just like it explains in the instructions.
Time taken :
Tools used :
AU$'s spent


I am itching to keep going but I NOW think there is merit in letting KTM-9 harden over the following weeks... just like it explains in the instructions.
Time taken :
Tools used :
AU$'s spent
Friday, November 03, 2006
Finish Finished
Or at least I hope so. Four days of finishing have past. In total I have 16 coats. Thats four coats a day, a light 360 grit sand back, then start again. It looks good but this time I will wait at least two weeks before I start taking of the tape.
Any way, I have put the KTM-9 up on the shelf until I am ready to finish the next one. I reckon you could finish three guitars with a quart of KTM-9. I have no hesitation in using this product or recommending it to other first time builders. I know I have nothing to compare it with by I am getting a finish that I would never have expected.
Time taken : another hour in total
Tools used : KTM-9
AU$'s spent : Nil
Any way, I have put the KTM-9 up on the shelf until I am ready to finish the next one. I reckon you could finish three guitars with a quart of KTM-9. I have no hesitation in using this product or recommending it to other first time builders. I know I have nothing to compare it with by I am getting a finish that I would never have expected.
Time taken : another hour in total
Tools used : KTM-9
AU$'s spent : Nil
Wednesday, November 01, 2006
Second Finish
Yesterday I put on four thin coats of KTM-9 and then this afternoon, I gave it a very light rub back - to bare wood again. I added in a tiny bit of the stain to the effected area, hiding it well. Then tonight I applied another four coats.
Seems to be coming along okay.
Time taken : 1 hour in total
Tools used : Paint brush KTM-9 360 grit paper
AU$'s spent : Nil
Seems to be coming along okay.
Time taken : 1 hour in total
Tools used : Paint brush KTM-9 360 grit paper
AU$'s spent : Nil
Monday, October 30, 2006
Day 92
That's right! I've been on this buid for getting close to a third of the year. And, I think I've been making fairly good time. Don't ever think that you'll wizz you way through the first build. I have no doubt that my second (and following ones) will be quicker as I will have a number of different processes going at the same time instead of following the pages in the manual
I'm feeling good about the buil again. Today I put on the two coats of stain again. Tomorrow I will start putting on the KTM-9 again. To think, I had planned to have this all done by mid November.
Still I am glad that I took the time and effort to restart the neck. I think it is better this time around. Practice makes presentable
Time taken : 1 hour
Tools used : sandpaper, stain, rags
AU$'s spent : Nil
I'm feeling good about the buil again. Today I put on the two coats of stain again. Tomorrow I will start putting on the KTM-9 again. To think, I had planned to have this all done by mid November.
Still I am glad that I took the time and effort to restart the neck. I think it is better this time around. Practice makes presentable
Time taken : 1 hour
Tools used : sandpaper, stain, rags
AU$'s spent : Nil
Sunday, October 29, 2006
Neck Setting - Again
Well I think I might be back on track. It’s not pretty but I have sanded back the neck and started again. That silly Martin diamond – I almost sanded the whole thing off. Then I went crazy making new shims and resetting the neck again. This time I (finger) tightly bolted the neck on before I took any measurements. I also tidied up a few of those blemishes that I have been frowning at since I started finishing the neck.
I took to my beautiful finish with paint stripper so that I will one day have a gluing surface under the fret board.
It’s late now but so I have stopped, tomorrow I might sand a little fret board relief into the top, like Kenneth Michael suggests.
Time taken : 4 hours
Tools used : sandpaper, craft knife, steel rules, superglue, mahogany
AU$'s spent : Nil
I took to my beautiful finish with paint stripper so that I will one day have a gluing surface under the fret board.
It’s late now but so I have stopped, tomorrow I might sand a little fret board relief into the top, like Kenneth Michael suggests.
Time taken : 4 hours
Tools used : sandpaper, craft knife, steel rules, superglue, mahogany
AU$'s spent : Nil
Friday, October 27, 2006
I give up.
Because I like to play with things I positioned the bridge today, taped it down and checked my neckset. It's out. The gap is about twice as much as I remember. What's going on? Angry Angry Angry
Time taken : Nil
Tools used : Nil
AU$'s spent : Nil
Time taken : Nil
Tools used : Nil
AU$'s spent : Nil
Thursday, October 26, 2006
More reading ahead
I've been sitting here thinking. I will have to strip it and start again. I might go back to reading about Tru-Oil and the like. Then again, I am now thinking that I did not leave the finish to cure long enough before leveling and final sanding.

Time taken :
Tools used :
AU$'s spent :

Time taken :
Tools used :
AU$'s spent :
I don't want to talk about it
but I will.
Once again I am reminded that I am a novice, a fool and a cocky idiot. As mentioned yesterday, I was on a high turning out this sort of result on the body...

So today, I start on the neck. Somehow, and I still have no idea how, I managed to sand through the KTM-9, it must have been so very thin. How did I manage to get through a dozen or so coats? I rubbed back the body fairly vigorously, trying to get out all of the shine, trying to make it as flat as possible and I think that I ended up with a great result. So today, I just took off mindlessly, following the same steps and then I look down and I see... light coloured mahogany.
THEN! I say to myself, "Self, you could hide that with a tiny bit of stain on a cotton wool tip, only you will know Self." - Drongo - Alcohol based stain EATS plastic KTM-9.
THEN! I notice that there are two spots on the fretboard edge that appear to have once been air bubbles under the KTM-9. I don't know, they weren't there/visable before.
THEN! I think "Let's try and buff that tiny spot out" so I start, following the same steps as I did on the body and... with a slip of the hand, I let the chuck of a high speed spinning drill drag along the neck, leaving two great big scratches.
THEN! I pull off the masking tape. No matter how slow, gentle or controlled I tried to be, I pulled the KTM away as well. Let me tell you - It is thick. I don't get it.
I have sort of calmed down - I can not find my memory card at the moment (honest) but I promise I will show you all the mistakes ASAP. That neck will have to be stripped back and done again... one day.
At the moment, I am thinking about moving on and coming back to it.... after I've heard the guitar - I CAN NOT WAIT. I can't foresee any steps from here on in that will prevent me from going back and re-finishing the neck.
Time taken : 1 hour
Tools used : drill, buff, wood polishing compound, sandpaper,
AU$'s spent : Nil
Once again I am reminded that I am a novice, a fool and a cocky idiot. As mentioned yesterday, I was on a high turning out this sort of result on the body...

So today, I start on the neck. Somehow, and I still have no idea how, I managed to sand through the KTM-9, it must have been so very thin. How did I manage to get through a dozen or so coats? I rubbed back the body fairly vigorously, trying to get out all of the shine, trying to make it as flat as possible and I think that I ended up with a great result. So today, I just took off mindlessly, following the same steps and then I look down and I see... light coloured mahogany.
THEN! I say to myself, "Self, you could hide that with a tiny bit of stain on a cotton wool tip, only you will know Self." - Drongo - Alcohol based stain EATS plastic KTM-9.
THEN! I notice that there are two spots on the fretboard edge that appear to have once been air bubbles under the KTM-9. I don't know, they weren't there/visable before.
THEN! I think "Let's try and buff that tiny spot out" so I start, following the same steps as I did on the body and... with a slip of the hand, I let the chuck of a high speed spinning drill drag along the neck, leaving two great big scratches.
THEN! I pull off the masking tape. No matter how slow, gentle or controlled I tried to be, I pulled the KTM away as well. Let me tell you - It is thick. I don't get it.
I have sort of calmed down - I can not find my memory card at the moment (honest) but I promise I will show you all the mistakes ASAP. That neck will have to be stripped back and done again... one day.
At the moment, I am thinking about moving on and coming back to it.... after I've heard the guitar - I CAN NOT WAIT. I can't foresee any steps from here on in that will prevent me from going back and re-finishing the neck.
Time taken : 1 hour
Tools used : drill, buff, wood polishing compound, sandpaper,
AU$'s spent : Nil
Wednesday, October 25, 2006
Gee. I'm good
Now I am not saying that I am a pro but I am really impressed with my result. I rubbed the body back to nearly flat with 360 grit paper and then wet-n-dry at 1200 grit and then again at 2000 grit.
By that stage I thought that I was almost back to bare wood, it looked too my eye there did not appear to be any KTM-9 left and I started to worry.
Then I took to the body with a polishing compound and buff on the electric drill and up it came. Lovely flat shine. I'll show you the photos once I've completed the body and the neck. Stay tuned.
Time taken : 2 hours
Tools used : Electric Drill, cloth buff, polishing compound
AU$'s spent : $18.95 polishing compound, $28.00 cloth buff, $8.00 sand paper
By that stage I thought that I was almost back to bare wood, it looked too my eye there did not appear to be any KTM-9 left and I started to worry.
Then I took to the body with a polishing compound and buff on the electric drill and up it came. Lovely flat shine. I'll show you the photos once I've completed the body and the neck. Stay tuned.
Time taken : 2 hours
Tools used : Electric Drill, cloth buff, polishing compound
AU$'s spent : $18.95 polishing compound, $28.00 cloth buff, $8.00 sand paper
Saturday, October 21, 2006
Getting closer to the finish finish
Craig has asked for an update about the finishing process so I thought I would post a few progressive photos. I am starting to get the hang on brushing on the KTM-9. I am confident that the thinking of less is best is the way to go. I was trying to get thick and well covering layers of lacquer on each time but I have found that the bubbles or drips that go along with the thicker coats are harder to deal with once they have dried.
I also found that the KTM tacks off rather quickly and touching the area again can result in disaster. The latest coats have been thin, light and imperfect but I no longer have drips or air bubbles.
I have now applied about ten or twelve coats now and rubbed back the higher points with 340 paper about every 3 or 4 coats. I’ve also noted that the sand paper doesn’t seem to last very long – which was surprising. I am most likely using the wrong type of paper.
The photos below I took today and I am thinking that tonight, I will sand the surfaces back until there is no shine left of the surface. Please keep in mind that with these photos I have tried to take images which show the flaws in the finish. I have turned the piece so that all the brush marks and thin parts are visible.
In general I am happy with my first effort at finishing. Those that have seen the guitar have all commented on how good the product looks. Maybe next time (planning is underway) I will spray but I think that brushing KTM-9 is suitable for the home builder to brush on.



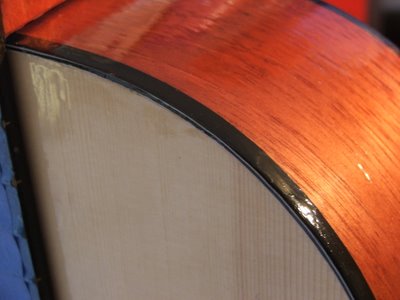
Time taken :
Tools used :
AU$'s spent :
I also found that the KTM tacks off rather quickly and touching the area again can result in disaster. The latest coats have been thin, light and imperfect but I no longer have drips or air bubbles.
I have now applied about ten or twelve coats now and rubbed back the higher points with 340 paper about every 3 or 4 coats. I’ve also noted that the sand paper doesn’t seem to last very long – which was surprising. I am most likely using the wrong type of paper.
The photos below I took today and I am thinking that tonight, I will sand the surfaces back until there is no shine left of the surface. Please keep in mind that with these photos I have tried to take images which show the flaws in the finish. I have turned the piece so that all the brush marks and thin parts are visible.
In general I am happy with my first effort at finishing. Those that have seen the guitar have all commented on how good the product looks. Maybe next time (planning is underway) I will spray but I think that brushing KTM-9 is suitable for the home builder to brush on.



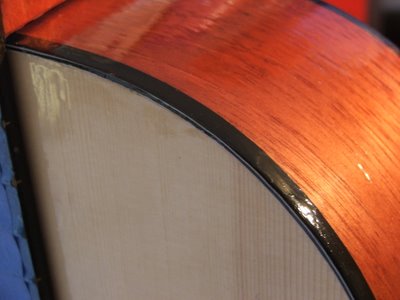
Time taken :
Tools used :
AU$'s spent :
Tuesday, October 17, 2006
Closer to the end
Another few coats of KTM-9 went on tonight but a majority of the evening has been taken up because I finally gathered the courage to add up the total $AUD I have spent whilst making this guitar. It is an interesting amount. I will report as to the cost, tools used and number of hours soon.
Time taken :
Tools used :
AU$'s spent :
Time taken :
Tools used :
AU$'s spent :
Monday, October 16, 2006
Finishing Woes
I am getting frustrated, basically because I have no idea what I am doing. I have all but lost count of how many coats of KTM-9 I have brushed on, I'll say seven. The first few went on really well, smooth and with next to no brush marks.
It may be because the surface is less absorptive now but no matter how I let the body "rest", I am getting bubbles where the finish pools, following gravity. I have tried brushing thinner but I find that as I brush the coat thinner, the lacquer gets tacky and then the brush marks increase and/or I get small pieces of lacquer rolling up into tiny gel like balls.
When I try to take back the hardened bubbles, I end up bursting through and it leaves a concaved surface.
I am sure this all has more to do with operator error as opposed to it being an issue with the product. I scuffed back with 340 grit after the first three coats. I think I might start moving up through the higher number grade papers tomorrow.
If any of the readers out there have brushed on KTM-9 before, I love to know what steps you took and how you finished it all off. Please leave a comment.
Time taken : About 2 hours, it doesn't take long for each coat.
Tools used : brush, KTM-9, sand paper
AU$'s spent : Nil
It may be because the surface is less absorptive now but no matter how I let the body "rest", I am getting bubbles where the finish pools, following gravity. I have tried brushing thinner but I find that as I brush the coat thinner, the lacquer gets tacky and then the brush marks increase and/or I get small pieces of lacquer rolling up into tiny gel like balls.
When I try to take back the hardened bubbles, I end up bursting through and it leaves a concaved surface.
I am sure this all has more to do with operator error as opposed to it being an issue with the product. I scuffed back with 340 grit after the first three coats. I think I might start moving up through the higher number grade papers tomorrow.
If any of the readers out there have brushed on KTM-9 before, I love to know what steps you took and how you finished it all off. Please leave a comment.
Time taken : About 2 hours, it doesn't take long for each coat.
Tools used : brush, KTM-9, sand paper
AU$'s spent : Nil
Monday, October 09, 2006
Spray Handles
In answer to Greg's question, I have used the broken waste clamp as a spray handle. I used one of the 8 inch rods from the clamps I had made to glue down the top and bottom to attached the clamp to the neck block. It has worked out well, I have a small clamp that rotates as well, this enables me to turn the body as I apply the finish. The neck I have simply attached to a length of wood.

I have scuffed back the first coat of lacquer and applied another two layers on top since. It seems to be all coming along nicely. Touch wood
Time taken : 30 minutes
Tools used : brushes, KTM-9, sandpaper
AU$'s spent : Nil

I have scuffed back the first coat of lacquer and applied another two layers on top since. It seems to be all coming along nicely. Touch wood
Time taken : 30 minutes
Tools used : brushes, KTM-9, sandpaper
AU$'s spent : Nil
Friday, October 06, 2006
The Finish Goes On
Perhaps it won't be the best finish put on by an novice, but I have decided to press ahead and just start with the KTM-9 finish - and I am brushing it on.

Obviously the blog will slow down for a while now as it would be a bit pointless to tell you all about each coat and the days of drying in between
Time taken : 30 minutes
Tools used : brush, KTM-9
AU$'s spent : Nil

Obviously the blog will slow down for a while now as it would be a bit pointless to tell you all about each coat and the days of drying in between
Time taken : 30 minutes
Tools used : brush, KTM-9
AU$'s spent : Nil
Tuesday, October 03, 2006
I'm an idiot
I read the instruction manual, I read the bit where it said "mask the sound board" and in a lot of respects I did. I masked of about three edges all the way around, heaps. It worked fine for the first three applications of the stain and then tonight I had a totally brain melt down and for some reason I thought it would support the guitar by placing a couple of stain covered fingers in the middle of the sound board.
I am an idiot.
This idiot has also been think about setting the neck again... considering how much sanding I have done to the neck block area etc. Did not dare look at it tonight. Left the workshop fairly angry tonight.
Time taken : 10 minutes
Tools used : stain, rag, stupidity
AU$'s spent : nil
I am an idiot.
This idiot has also been think about setting the neck again... considering how much sanding I have done to the neck block area etc. Did not dare look at it tonight. Left the workshop fairly angry tonight.
Time taken : 10 minutes
Tools used : stain, rag, stupidity
AU$'s spent : nil
Moving right along
I got stuck into all that white wood filler with the sand paper and took it all back to bare wood again. The only places that the filler remains is where I made horrible (but little) mistakes, places where there was a gap between the wood and the binding for example.
Then I put back on the first coat of stain.
You really notice how your technique improves the second time around. You can practice and practice on scrap wood but there is something different about putting wood stain onto your guitar... it seems a lot more "fluid"
The wood putty coloured up okay - it was just a brighter pink.
Might get the second coat of stain on before bed tonight. Honestly, If I could have, if the build was flawless, I would not stain the mahogany. When I wet the wood to raise the grain, that is the way I would like the wood to look the whole time. I can however acknowledge that the stain will hide some of those little marks and knocks that I have pick up along the way.
Time taken : 2 hours
Tools used : sandpaper, electric sander, stain
AU$'s spent : nil
Then I put back on the first coat of stain.
You really notice how your technique improves the second time around. You can practice and practice on scrap wood but there is something different about putting wood stain onto your guitar... it seems a lot more "fluid"
The wood putty coloured up okay - it was just a brighter pink.
Might get the second coat of stain on before bed tonight. Honestly, If I could have, if the build was flawless, I would not stain the mahogany. When I wet the wood to raise the grain, that is the way I would like the wood to look the whole time. I can however acknowledge that the stain will hide some of those little marks and knocks that I have pick up along the way.
Time taken : 2 hours
Tools used : sandpaper, electric sander, stain
AU$'s spent : nil
Monday, October 02, 2006
Back to Square One
I remember a couple of weeks ago, when I was setting the neck, and getting it all wrong. I was getting close to putting the whole thing into the chipper. Tonight I am ready to put myself in.
I was feeling really comfortable with the way the finishing was progressing. I still felt that there was a little too much red, but already the colour (Australians spell colour correctly) was growing on me.

Then, I moved on to the pore filling and this is where I have totally mucked up – this is where the master wood workers would have been good to have around.
Now, I’ve never used pore/wood filler before. I’ve heard and read that on most occasions they are easy to sand back and the instructions on the product I used simply said something like “spread with a plastic scraper”. I went in thinking that I couldn’t really overdose on the filler. I thought that if I used too much I could simply sand it back.
To compound this – Neutral is not – It is white – and it looks really bad on mahogany.

As soon as I started sanding it back, I started wearing off the stain on the edges. I could see that I was going to leave the surface
My only option now is to rub it all back and start again. Great – No doubt next I’ll sand right though. Did I ever mention that I love sanding?
Time taken : 1.5 hours
Tools used : plastic spatula, wood filler, sand paper
AU$'s spent : Nil
I was feeling really comfortable with the way the finishing was progressing. I still felt that there was a little too much red, but already the colour (Australians spell colour correctly) was growing on me.

Then, I moved on to the pore filling and this is where I have totally mucked up – this is where the master wood workers would have been good to have around.
Now, I’ve never used pore/wood filler before. I’ve heard and read that on most occasions they are easy to sand back and the instructions on the product I used simply said something like “spread with a plastic scraper”. I went in thinking that I couldn’t really overdose on the filler. I thought that if I used too much I could simply sand it back.
To compound this – Neutral is not – It is white – and it looks really bad on mahogany.

As soon as I started sanding it back, I started wearing off the stain on the edges. I could see that I was going to leave the surface
My only option now is to rub it all back and start again. Great – No doubt next I’ll sand right though. Did I ever mention that I love sanding?
Time taken : 1.5 hours
Tools used : plastic spatula, wood filler, sand paper
AU$'s spent : Nil
Sunday, October 01, 2006
A second coat
Tonight I put on a second coat of the stain in an attempt to darken the redness - there was almost a pinkish tinge that I wanted to darken over. Gee I wish I could have pressed pause when I put on the second coat. When it was wet, the stain had a kind of honeycomb appearance about it... and then it faded away as it dried.
Just to remind me that I don't know what I am doing, the second coat has highlighted glue marks that I couldn't see before - nothing major, just annoying.
Time taken : 10 minutes
Tools used : Stain, rag, glove
AU$'s spent : nil
Just to remind me that I don't know what I am doing, the second coat has highlighted glue marks that I couldn't see before - nothing major, just annoying.
Time taken : 10 minutes
Tools used : Stain, rag, glove
AU$'s spent : nil
Saturday, September 30, 2006
The Stain Goes On
Okay - Which one of you forgot to mention that stains dissolve rubber glove? What is the point in wearing them when the rubber breaks down in the first five minutes. My finger tips are now nicely stained as well.
Although striking, I am not really happy with the result. I put the stain on really thin and even though it looked okay when it was wet, it is drying too light in some places and it appears patchy.
I am concerned that a second application may make it too dark.

Time taken : half an hour
Tools used : masking tape, stain, thinner, rag, glass jar, rubber gloves
AU$'s spent : nil
Although striking, I am not really happy with the result. I put the stain on really thin and even though it looked okay when it was wet, it is drying too light in some places and it appears patchy.
I am concerned that a second application may make it too dark.

Time taken : half an hour
Tools used : masking tape, stain, thinner, rag, glass jar, rubber gloves
AU$'s spent : nil
Wednesday, September 27, 2006
Creating the nut

I spent last night shaping the nut and getting it into place. I had not idea how I was going to make the 15 degree angle, using the old school protractor. I ended up using a flat piece of scrap with sand paper on it and another block underneath to raise the scrap to the angle of the neck. I then used my highly calibrated eye to hold the nut straight up and down whilst rubbing in the angle.
That ended up being quite rough so I cut slithers of sand paper and finished the nut by pulling the sandpaper between the neck and the nut.

Time taken : 2 hours
Tools used : sand paper, scrap wood, chisel, pencil
AU$'s spent : nil
Sunday, September 24, 2006
I don't like sanding - but I like the results
The inlay is done and I am fairly happy with my first ever effort. It would have worked out so much better had I of not dropped and shattered the pearl and if I had of glued it down before adding the epoxy. Notes for next time.

Now these photos give you an up close, warts and all view of the result. To the naked eye at arms length, it is not really visible at all. I recommend a simple inlay to everyone making a guitar. It is not as difficult as I have most likely made it sound and even huge mistakes like mine come up okay. If I was to do it again, I would firstly, forget all about trying to make my own design and then remember to respect how delicate that pearl stuff is. Next time, I am going to get some dentist drill bits to put into the Dremel. I think the smaller the piece the better. I was trying to go very slow but still managed to botch it up because the cutting edge of the bit was not as deep as the groove required. I was actually cutting a few mm (or smaller) past the line, underneath, but from above I could still see the line.

The frets also came up quite well and I think that most of the cover up work is done.

I am getting closer and closer to that finishing stage.
Time taken : .5 hours
Tools used : sandpaper, electric sander
AU$'s spent : Nil

Now these photos give you an up close, warts and all view of the result. To the naked eye at arms length, it is not really visible at all. I recommend a simple inlay to everyone making a guitar. It is not as difficult as I have most likely made it sound and even huge mistakes like mine come up okay. If I was to do it again, I would firstly, forget all about trying to make my own design and then remember to respect how delicate that pearl stuff is. Next time, I am going to get some dentist drill bits to put into the Dremel. I think the smaller the piece the better. I was trying to go very slow but still managed to botch it up because the cutting edge of the bit was not as deep as the groove required. I was actually cutting a few mm (or smaller) past the line, underneath, but from above I could still see the line.

The frets also came up quite well and I think that most of the cover up work is done.

I am getting closer and closer to that finishing stage.
Time taken : .5 hours
Tools used : sandpaper, electric sander
AU$'s spent : Nil
Saturday, September 23, 2006
Filling the Frets
This morning I started to sand back the epoxy of the inlay. I didn't finish it off totally, I'll get to that tomorrow as I have some time for a big out doors sanding session. I am starting to think it will come out okay.

Tonight I filled the gaps under the frets. The first time I tried using the black superglue but being about as thick as water, it just rolled down into the slot and left the gap there.
I had put aside a whole heap of fretboard dust from when I was "shooting the board" I mixed that into the clear epoxy and being thicker that appears to have worked quite well.

My ambition may have out weighed my ability. While I had the fret board coloured epoxy out, I thought to myself, "Why don't I hide some of those file marks on the sides" Time will tell.
Time taken : 1 hour
Tools used : black super glue, epoxy, toothpick, pin, sandpaper.
AU$'s spent : Nil

Tonight I filled the gaps under the frets. The first time I tried using the black superglue but being about as thick as water, it just rolled down into the slot and left the gap there.
I had put aside a whole heap of fretboard dust from when I was "shooting the board" I mixed that into the clear epoxy and being thicker that appears to have worked quite well.

My ambition may have out weighed my ability. While I had the fret board coloured epoxy out, I thought to myself, "Why don't I hide some of those file marks on the sides" Time will tell.
Time taken : 1 hour
Tools used : black super glue, epoxy, toothpick, pin, sandpaper.
AU$'s spent : Nil
Thursday, September 21, 2006
Inlay Goes On
What have I done? Only time will tell. I may have just ruined the appearance of my guitar, then again it may come out okay. I've added a few more photos of this step, just to give a better idea of what I did.
I started out by super gluing the pearl in place and then used a craft knife to trace around the outside, leaving me with an outline.
It was during this process that I dropped the inlay on the ground and it shattered into two.... and my blood pressure started to climb.

Then it all went totally pair shaped. The edges of the pearl were not square and although I spent ages, taking my time, working the edges out, I still managed to stuff it up, taking away wood in the wrong places.

Needless to say, my blood was beginning to boil.

Not being able to take a backwards step, I was left with only one option. I got the sandpaper out and rubbed down scraps left over from the overlay and then mixed some clear expoxy and tinted it with the dust.

The plan is that when I rub it back tomorrow, it'll be perfect and you'll never be able to notice that the job was completed by a mere amateur.
Ten minutes after the last photo I thought to myself, "I should have glued that down, I hope the expoxy holds it in place"
Time taken : 2.5 hours
Tools used : craft knife, super glue, epoxy, sandpaper
AU$'s spent : Nil
I started out by super gluing the pearl in place and then used a craft knife to trace around the outside, leaving me with an outline.
It was during this process that I dropped the inlay on the ground and it shattered into two.... and my blood pressure started to climb.

Then it all went totally pair shaped. The edges of the pearl were not square and although I spent ages, taking my time, working the edges out, I still managed to stuff it up, taking away wood in the wrong places.

Needless to say, my blood was beginning to boil.

Not being able to take a backwards step, I was left with only one option. I got the sandpaper out and rubbed down scraps left over from the overlay and then mixed some clear expoxy and tinted it with the dust.

The plan is that when I rub it back tomorrow, it'll be perfect and you'll never be able to notice that the job was completed by a mere amateur.
Ten minutes after the last photo I thought to myself, "I should have glued that down, I hope the expoxy holds it in place"
Time taken : 2.5 hours
Tools used : craft knife, super glue, epoxy, sandpaper
AU$'s spent : Nil
Tuesday, September 19, 2006
Should I Inlay?
Today the mail arrived and there was the box containing the mother of pearl inlays I had order last week. Luckily, I ordered three letter "W"'s because one of them had a hairline fracture in the face. It was not a mail issue as there was no damage to the box.
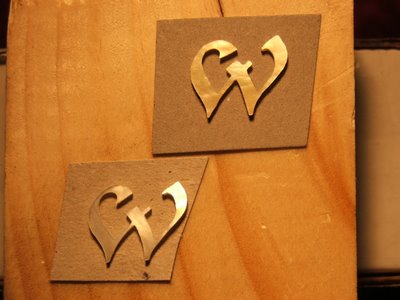
I sat down and started trying to inlay the pearl into a piece of scrap pine (much softer than mahogany) with the Dremel and let me tell you, I am no more confidant than I was last week.

I really don't know if I should go ahead and try this out - worried... but then again I've been there before on this project.
I think it would look good if I manage to get it in there somewhat neatly.

Time taken : Nil
Tools used : Dremel, scrap wood, craft knife, pencil
AU$'s spent : Nil
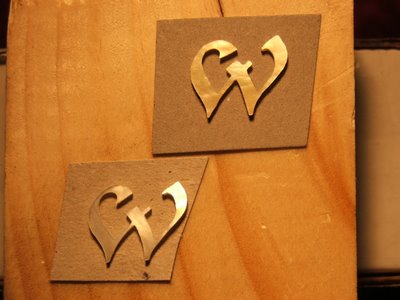
I sat down and started trying to inlay the pearl into a piece of scrap pine (much softer than mahogany) with the Dremel and let me tell you, I am no more confidant than I was last week.

I really don't know if I should go ahead and try this out - worried... but then again I've been there before on this project.
I think it would look good if I manage to get it in there somewhat neatly.

Time taken : Nil
Tools used : Dremel, scrap wood, craft knife, pencil
AU$'s spent : Nil
Monday, September 18, 2006
Anymore To Spend?
This might be a little presumptuous of me to say this but I think that I might have spent the last dollar needed to build this guitar... I am certainly not planning on spending any more. Could this be true? I have deliberately not added up the cost - in fear of what the answer will be.
I've grabbed a mahogany stain and a reducer to make it lighter as possible. The folk at Compliant Spray Systems never got back to me so I just bit the bullet and scooped a local product off the shelf, I'll try the neutral Red Devil wood filler.

In other news I set the last frets into the board last night. I had a reminder of my skill level. I whacked my finger with the hammer, jamming in on a fret. I am now sporting a really great blood blister - couldn't even play a guitar tonight if I wanted to.
Time taken : Nil
Tools used : Nil
AU$'s spent : Wattyl Mahogany stain $15.43, Wattyl reducer $9.53, Red Devil Wood Filler $8.10
I've grabbed a mahogany stain and a reducer to make it lighter as possible. The folk at Compliant Spray Systems never got back to me so I just bit the bullet and scooped a local product off the shelf, I'll try the neutral Red Devil wood filler.

In other news I set the last frets into the board last night. I had a reminder of my skill level. I whacked my finger with the hammer, jamming in on a fret. I am now sporting a really great blood blister - couldn't even play a guitar tonight if I wanted to.
Time taken : Nil
Tools used : Nil
AU$'s spent : Wattyl Mahogany stain $15.43, Wattyl reducer $9.53, Red Devil Wood Filler $8.10
Sunday, September 17, 2006
I Don't Get It
I'm back on track. Those shims seemed to have worked fairly well, I think that after final sanding and the once the finish is on, the hole mess will be hidden well enough.
However I am left with a burning question. How did it go so wrong? The shims I made were from the same piece of wood, they were the same thickness. I glued one on either side so in theory, the whole neck should be raised and basically the neck set should remain the same.
I was amazed when I checked the side to side and saddle height after taking the wax paper out. The measurements are now even and I am fairly happy with them. I'd like to bring the neck a tiny bit more forward but maybe I should just be happy with what I have at the moment.
Time taken : Nil
Tools used : Nil
AU$'s spent : Nil
However I am left with a burning question. How did it go so wrong? The shims I made were from the same piece of wood, they were the same thickness. I glued one on either side so in theory, the whole neck should be raised and basically the neck set should remain the same.
I was amazed when I checked the side to side and saddle height after taking the wax paper out. The measurements are now even and I am fairly happy with them. I'd like to bring the neck a tiny bit more forward but maybe I should just be happy with what I have at the moment.
Time taken : Nil
Tools used : Nil
AU$'s spent : Nil
Saturday, September 16, 2006
Making Things Right
I've been thinking and worked out that the only way I could start to fix the problem is by shimming the cheeks on the neck and thereby putting some space in between the neck and the block again - no matter how slight that would space will be.
In the Stewmac bolt on kit, you also receive the mahongany that would have been required for the shims for the dovetail, this is the wood I used. Basically I traced the profile of cheeks and then made a shim about 5mm wide - the width of the shim. I glued them in place, leaving a slight overhang to sand back and blend in the neck, and using wax paper I used the body of the guitar and pressure on the bolts for clamping.

Hope it works.
Time taken : 20 minutes
Tools used : glue, craft knife
AU$'s spent : nil
In the Stewmac bolt on kit, you also receive the mahongany that would have been required for the shims for the dovetail, this is the wood I used. Basically I traced the profile of cheeks and then made a shim about 5mm wide - the width of the shim. I glued them in place, leaving a slight overhang to sand back and blend in the neck, and using wax paper I used the body of the guitar and pressure on the bolts for clamping.

Hope it works.
Time taken : 20 minutes
Tools used : glue, craft knife
AU$'s spent : nil
Thursday, September 14, 2006
Driving Me Crazy
I am tearing my hair out! I get the side to side right, then I muck that up trying to get the tilt right. I bought the sides down so much that I ended up with a hump in middle of the heal on the neck... level that and then the side to side AND the tilt were out.... almost back at square one. At this rate, I am not going to have a neck left after another twenty nights of shaving it away. I am getting very angry. The edges of the neck are not even touching the sides. I've been pushing down on the neck so much that I have pressed flat smooth places on to the sides. I will not settle for a high action - I hate high actions.
I'm wild - I am sure that the bottom of the tenon is now touching on mortise within the neck block (Is that the right way around?) and any further adjustments I make will just make the joint looser, messier and even harder to set.


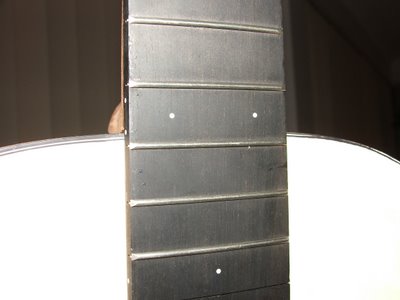
Notice how the 12th fret is now lower than the edge of the body.
Frustrated, angry, confused and doubting my ability. I give up tonight.
Time taken : 2.5 Hours
Tools used : same as last night
AU$'s spent : Nil (but I'd pay to have that neck perfect).
I'm wild - I am sure that the bottom of the tenon is now touching on mortise within the neck block (Is that the right way around?) and any further adjustments I make will just make the joint looser, messier and even harder to set.


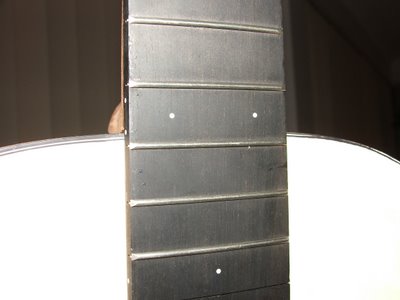
Notice how the 12th fret is now lower than the edge of the body.
Frustrated, angry, confused and doubting my ability. I give up tonight.
Time taken : 2.5 Hours
Tools used : same as last night
AU$'s spent : Nil (but I'd pay to have that neck perfect).
Wednesday, September 13, 2006
Neck Is Just About Set
I spent my time tonight slowly etching away, adjusting the neck, trying to get it set right. I think I have it fairly close. I’ve reached that point where I think, should I go any further? I’ll leave it and take another look with a set of fresh eyes tomorrow.
I must say, I expected that the neck joint would have been tighter, but this seems to be a common complaint – I had a few millimeters of sideways movement, allowing twist. I found that the measurements would change without taking any wood off.
Next time around, I don’t think I do too much sanding before setting the next, except obviously the areas that affect the measurements. – I’ve whacked my guitar a few dozen times with my straight edge tonight.
Still either way, in the corner of the room, there is a construction that definitively looks like a guitar.
Time taken : 3 hours
Tools used : chisel, sand paper, craft knifes, straight edge, rulers
AU$'s spent : Nil
I must say, I expected that the neck joint would have been tighter, but this seems to be a common complaint – I had a few millimeters of sideways movement, allowing twist. I found that the measurements would change without taking any wood off.
Next time around, I don’t think I do too much sanding before setting the next, except obviously the areas that affect the measurements. – I’ve whacked my guitar a few dozen times with my straight edge tonight.
Still either way, in the corner of the room, there is a construction that definitively looks like a guitar.
Time taken : 3 hours
Tools used : chisel, sand paper, craft knifes, straight edge, rulers
AU$'s spent : Nil
Tuesday, September 12, 2006
An Aussie Alternative
Wow. I've heard of this Enduro product for pore filling before finishing. The folk from Compliant Spray Systems have quoted me $65-$85 in freight to get it Down Under. Is that US dollars or AUD?... gee I hope is Peso. The product itself only cost US$16 odd dollars to buy.
I think there has to be a suitable local product - can anyone help?
Time taken : Nil - Not yet
Tools used : Nil
AU$'s spent : Nil
I think there has to be a suitable local product - can anyone help?
Time taken : Nil - Not yet
Tools used : Nil
AU$'s spent : Nil
Monday, September 11, 2006
Slowly Does It
I watched the video a couple of times, read the book over and over and then started to chisel out the "cheeks" on the end of the neck heel. I've tried and tried to sharpen chisels but I am really bad at it. I ended up reverting to my craft knife kit, making the cuts smaller and therefore the mistakes less.
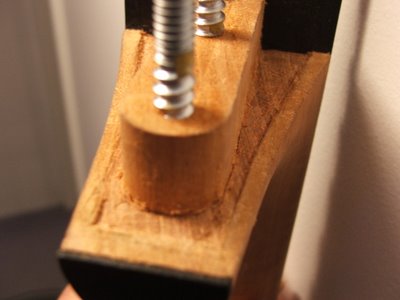
Tomorrow I will start shaving and sanding back the sides to get the centre line and then take some wood off the top on each side to try and bring the neck angle forward.
Wish me luck?
Time taken : 2 hours
Tools used :
AU$'s spent :
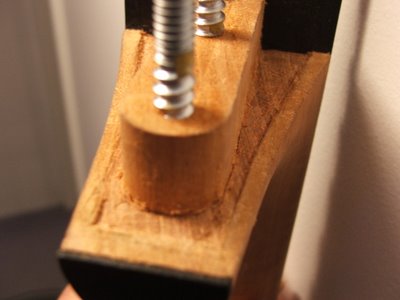
Tomorrow I will start shaving and sanding back the sides to get the centre line and then take some wood off the top on each side to try and bring the neck angle forward.
Wish me luck?
Time taken : 2 hours
Tools used :
AU$'s spent :
Subscribe to:
Posts (Atom)