Regular readers will know that I have spent a fair bit of time (and money) in my local Bunnings store of late. Tonight I took my two daughters to Bunnings for a Fathers Day craft workshop.
Now I have no corporate experience, I know little about running a business and I am not old enough to remember "the good ol' days" (I don't think) but this is something that I don't think you'll find in a business text book anywhere these days. When was the last time that you saw a large company, openly showing what I have dubbed Corporate Kindness.... apparently, it used to be common place and slid past the accountants under the title, good will.
Tonight I made two tool boxes with my daughters. One is for a grandfather, the other is for their mother (?). I am unable to explain how impressed I am with the staff and their efforts. Not only did the company supply the hardware, the paint and the three staff members, they also arranged dinner, drinks, mini golf and at least one gift for everyone that attended.
All that was expected of us was to have a good time and take home a happy memory - and if possible, a completed toolbox.
Rare to say the least. Bravo I say.
Time taken : Nil
Tools used : Nil
AU$'s spent : Nil
Thursday, August 31, 2006
Happy Again
I really don't know what you were all so worried about. I always knew that those bindings would work out okay. They are not great but I am impressed that they are not as bad as I was expecting. I found as I scraped back, the white/black/white bindings suddenly appeared. I did not get all the black smudges off the sound board but they have certainly improved and I expect that they will disappear during sanding.

For some reason the binding did not take in two places at the neck block so I have reglued them. Perhaps there was left over glue from glueing on the blocks.
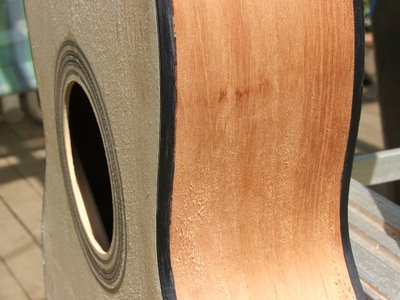
The answer to last nights quiz? I forgot to glue in the binding along the tail block, the end wedge. The end result is not a tight as it should be but it is okay.

Time taken : 1.5 hours
Tools used : scraper, craft knife, Weldon 16
AU$'s spent : Nil

For some reason the binding did not take in two places at the neck block so I have reglued them. Perhaps there was left over glue from glueing on the blocks.
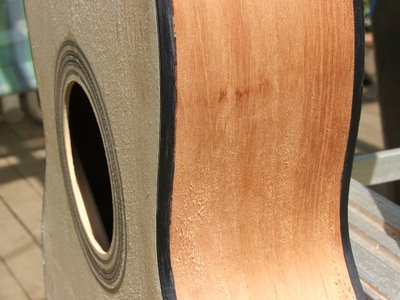
The answer to last nights quiz? I forgot to glue in the binding along the tail block, the end wedge. The end result is not a tight as it should be but it is okay.

Time taken : 1.5 hours
Tools used : scraper, craft knife, Weldon 16
AU$'s spent : Nil
Wednesday, August 30, 2006
Off Topic : People can play
Thanks to Earl, I've revisted this link.
Now, I am not really a fan of screaming or distorted guitar work however this guy has a lot of skill. A great demonstration of a few techniques, I won't ever get around to mastering. I survive on the belief that this kid has rote learnt this number and that he can't strum out three chords.
I started surfing YouTube looking for other players or what not that took my fancy. I really liked this guy, if you've ever tried to play a uke, you'll understand that this is a great effort
Time taken : Nil
Tools used : Nil
AU$'s spent : Nil
Now, I am not really a fan of screaming or distorted guitar work however this guy has a lot of skill. A great demonstration of a few techniques, I won't ever get around to mastering. I survive on the belief that this kid has rote learnt this number and that he can't strum out three chords.
I started surfing YouTube looking for other players or what not that took my fancy. I really liked this guy, if you've ever tried to play a uke, you'll understand that this is a great effort
Time taken : Nil
Tools used : Nil
AU$'s spent : Nil
Guess What I Forgot
I'm offering a dust pan of saw dust for the first person that can identify what I have done wrong, what I have left out.
I spend most of my day thinking about the guitar (sorry boss) and then I just race ahead as soon as I get home. I have to remember to stop reading ahead with the instruction manual.
Spent an hour in the shed, trying to cover my blue. Can you guess what it was?
Time taken : 1 hour
Tools used : craft knife, Dremel, superglue, Weldon 16, chisel
AU$'s spent : Nil
I spend most of my day thinking about the guitar (sorry boss) and then I just race ahead as soon as I get home. I have to remember to stop reading ahead with the instruction manual.
Spent an hour in the shed, trying to cover my blue. Can you guess what it was?
Time taken : 1 hour
Tools used : craft knife, Dremel, superglue, Weldon 16, chisel
AU$'s spent : Nil
In Two minds
Well... Let me say, it's not pretty. I am feeling a little flat but it is certainly not as bad as I was expecting. The Weldon 16 is a seriously effective product. The bindings have literally melted together and filled gaps between the binding and the wood.
The scotch guard masking tape that I used seems to have done the job very well, applying enough pressure over night but at the same time, it peeled off without too much drama at all.
Below is a picture of one of the ugliest places, the adhesive is obviously too thick in this place. Not to mentioned the black smudges on the sound board.
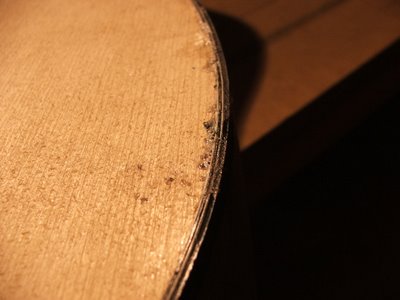
I these following photos are closer to the the kind of result I should have got all the way around.


Time taken : 20 minutes
Tools used : hairdryer
AU$'s spent : Nil
The scotch guard masking tape that I used seems to have done the job very well, applying enough pressure over night but at the same time, it peeled off without too much drama at all.
Below is a picture of one of the ugliest places, the adhesive is obviously too thick in this place. Not to mentioned the black smudges on the sound board.
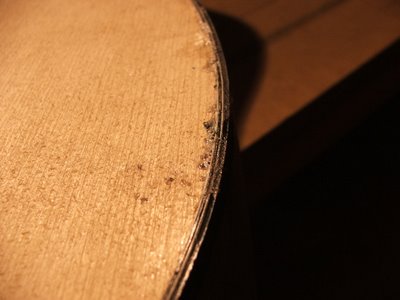
I these following photos are closer to the the kind of result I should have got all the way around.


Time taken : 20 minutes
Tools used : hairdryer
AU$'s spent : Nil
Tuesday, August 29, 2006
Binding the Edges - Not Happy
Not happy!
I went to Mulford Plastics today and picked up two tubes of Weldon 16. They had it displayed on the front counter - like they were waiting for me to walk in and ask for it.

I zipped home after work, woofed down dinner and headed to the shed to decorate my body.
Now I have a 7 year old daughter and I've tried to plat or braid her waist length hair a million times, and failed to get a decent appearance on each attempt. Although I put a few different things in place, getting the white/black/white binding into place, in the right order, without crossing over etc is hard and it gets harder towards the end as the binding has been wound up for... well at least five weeks. My suggestion to those that follow is firstly get a binding that is already laminated or at least, unwind it when you open your kit so it has less spring in it when you go to work with it
I got cement everywhere and I mean everywhere - I am so glad that I followed Bill Cory's tip and covered the sides with tape before I got started. I got enough cement on the lid to upset me - the stuff running down the side would have sent me over the edge. I do think that I was using too much glue, I just lay down a decent bead and worked from there... any less and I do not think that I would have got coverage.
The other thing being that the Weldon 16 eats away at the plastic, I got the black on my fingers... I got the black on my sound board. I've spent weeks looking after that wood, it's now covered with cement and molten black plastic.

I will be much more comfortable if/when I manage to get that tape off and it has all stuck firmly.
Tonight - I am not happy!
Time taken :
Tools used : Masking tape, Weldon 16 cement
AU$'s spent : $11.00
I went to Mulford Plastics today and picked up two tubes of Weldon 16. They had it displayed on the front counter - like they were waiting for me to walk in and ask for it.

I zipped home after work, woofed down dinner and headed to the shed to decorate my body.
Now I have a 7 year old daughter and I've tried to plat or braid her waist length hair a million times, and failed to get a decent appearance on each attempt. Although I put a few different things in place, getting the white/black/white binding into place, in the right order, without crossing over etc is hard and it gets harder towards the end as the binding has been wound up for... well at least five weeks. My suggestion to those that follow is firstly get a binding that is already laminated or at least, unwind it when you open your kit so it has less spring in it when you go to work with it
I got cement everywhere and I mean everywhere - I am so glad that I followed Bill Cory's tip and covered the sides with tape before I got started. I got enough cement on the lid to upset me - the stuff running down the side would have sent me over the edge. I do think that I was using too much glue, I just lay down a decent bead and worked from there... any less and I do not think that I would have got coverage.
The other thing being that the Weldon 16 eats away at the plastic, I got the black on my fingers... I got the black on my sound board. I've spent weeks looking after that wood, it's now covered with cement and molten black plastic.

I will be much more comfortable if/when I manage to get that tape off and it has all stuck firmly.
Tonight - I am not happy!
Time taken :
Tools used : Masking tape, Weldon 16 cement
AU$'s spent : $11.00
Sunday, August 27, 2006
How to finish?
I've started researching finishes but I am not getting very far. I found 851 Guitar Lacquer from Durobond however I emailed them and discovered that although the lacquer itself was reasonably priced at AU$36.30 a litre however, TNT would charge AU$105.00 to move the same litre over to Perth. Unreasonable to say the least.
Time taken : Nil
Tools used : Nil
AU$'s spent : Nil
Time taken : Nil
Tools used : Nil
AU$'s spent : Nil
Routing out the binding channels
Today I conquered one of my remaining fears about guitar kit making, I routed out the binding channels. That just leaves fretting, inlays, shaping, finishing, setup left to worry about.
I ended up using the StewMac Precision Router Set which made my first routing experience quite simple. After about twenty practice runs, I was finally happy with the depth and width of the cut and off I went. No worries. I heard a couple of pops or bumps a couple of times but there was no tear outs or any damage.

The back however was a totally different issue. Making the five degree wedge was only as difficult as it was for the sanding board. Getting the wedge onto the router and still having room to set the bit without hitting the edge guide was near impossible – I don’t get it.

At the time I was listening to the radio and the Eagles losing caused me to go a little postal. I sat back stewing and starting thinking “5 degrees is next to nothing over that distance…. No one will notice…. It’s the back” I routed my back without the wedge – I’ll let you know the result end result but it doesn't look too bad now.
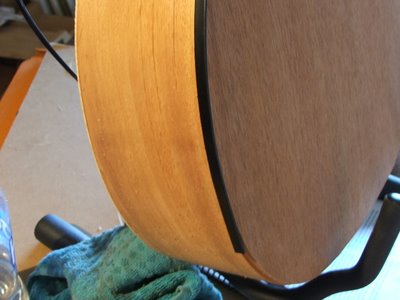
No all I have to do is find a glue to stick those bindings on with. That in itself it going to prove difficult – four pieces of plastic, wet with glue and lining them up and getting a finish that I can accept.
I couldn't get the weldon-16 cement that StewMac use because they can not export it. I've been doing research at my hardware store and bought some glues which I am doing small trials on. I have decided to follow Bill Cory's idea of covering the sides with low adhesive masking tape.
I've gone to the forum to find a substitute cement or glue for the bindings
Time taken : 2 hours
Tools used : Dremel, StewMac Router set, jigsaw, sand paper, scrap wood
AU$'s spent : $24.00 - masking tape, $7.35 - Kwik Grip sovlent based cement, $14.00 Titan Bond epoxy resin
I ended up using the StewMac Precision Router Set which made my first routing experience quite simple. After about twenty practice runs, I was finally happy with the depth and width of the cut and off I went. No worries. I heard a couple of pops or bumps a couple of times but there was no tear outs or any damage.

The back however was a totally different issue. Making the five degree wedge was only as difficult as it was for the sanding board. Getting the wedge onto the router and still having room to set the bit without hitting the edge guide was near impossible – I don’t get it.

At the time I was listening to the radio and the Eagles losing caused me to go a little postal. I sat back stewing and starting thinking “5 degrees is next to nothing over that distance…. No one will notice…. It’s the back” I routed my back without the wedge – I’ll let you know the result end result but it doesn't look too bad now.
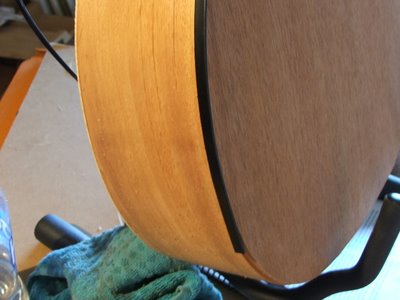
No all I have to do is find a glue to stick those bindings on with. That in itself it going to prove difficult – four pieces of plastic, wet with glue and lining them up and getting a finish that I can accept.
I couldn't get the weldon-16 cement that StewMac use because they can not export it. I've been doing research at my hardware store and bought some glues which I am doing small trials on. I have decided to follow Bill Cory's idea of covering the sides with low adhesive masking tape.
I've gone to the forum to find a substitute cement or glue for the bindings
Time taken : 2 hours
Tools used : Dremel, StewMac Router set, jigsaw, sand paper, scrap wood
AU$'s spent : $24.00 - masking tape, $7.35 - Kwik Grip sovlent based cement, $14.00 Titan Bond epoxy resin
Tuesday, August 22, 2006
What a poser !
I have become a poser. I spent a couple of hours in the shed this evening, thought about half an hour was spent standing back looking at my guitar. I got closer to finishing the edges off, getting ready for routing and then as a treat, I put the neck on, clamped the fret board in place just so I could have a look (and feel) what my guitar will finally look like.

Who would have thought a couple of months ago that I would be at this stage? Not me, that's for sure. If you are sitting back, reading this and wondering "could I, should I?" Then go for it - I can not explain the feeling, the first time you put it together and hold it like a guitar - Imagine what it will be like the first strum.
I have however remembered why I was never a big fan of wood work at school. I have very little patience, sanding wood for extended periods. I tend to lose interest very quickly and say to myself "that's enough" - That will not be acceptable.
When I took the chisel to the edges, I went too hard right in the curve of the waist and had a little bit of what I now know to be "tear out". I don't think it's too bad and I should be able to cover it with the binding.

I heard back from Perry, he has quoted $100.00 to inlay the 7 pieces into the fret board. I am still a little hung up on doing all this myself. I am going to give it a couple of days thought. Might have a play with the Dremel router when it arrives.
Time taken :1.5 Hours
Tools used : Chisel, sandpaper, craft knife
AU$'s spent : Nil

Who would have thought a couple of months ago that I would be at this stage? Not me, that's for sure. If you are sitting back, reading this and wondering "could I, should I?" Then go for it - I can not explain the feeling, the first time you put it together and hold it like a guitar - Imagine what it will be like the first strum.
I have however remembered why I was never a big fan of wood work at school. I have very little patience, sanding wood for extended periods. I tend to lose interest very quickly and say to myself "that's enough" - That will not be acceptable.
When I took the chisel to the edges, I went too hard right in the curve of the waist and had a little bit of what I now know to be "tear out". I don't think it's too bad and I should be able to cover it with the binding.

I heard back from Perry, he has quoted $100.00 to inlay the 7 pieces into the fret board. I am still a little hung up on doing all this myself. I am going to give it a couple of days thought. Might have a play with the Dremel router when it arrives.
Time taken :1.5 Hours
Tools used : Chisel, sandpaper, craft knife
AU$'s spent : Nil
Monday, August 21, 2006
Cole Clark Braces
I've spent a hundred hours + reading about making guitars. It appears that most makers have followed the standard cross brace method that I followed. Tonight I revisisted Cole Clark and took particular interest the way that he does his bracing and kerfing.
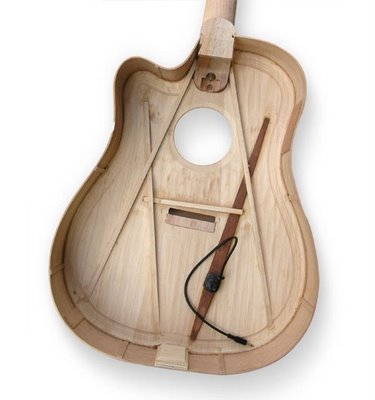
My soundbox is closed
I am over the moon. Tonight I pulled off all the clamps and held in my hands the closed sound box. When I held it up to the light there was not a single spec of light coming through. It feels strong and when I lay the back on a smooth surface it rocks both length ways and from side to side... it's even curved like it was designed to be.
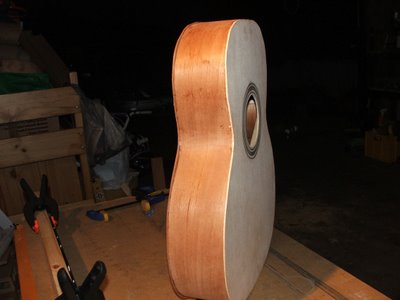
If you look hard, you can see where the kids wrote on the back, but you have to go looking for it.
Tonight I cleared out the top of the soundboard where the neck will attach and then I started to trim down the edges. This job, I suggest you do in phases because I found myself getting cocky with the chisel and really digging in. It would not take too much to drive the chisel right into the sides.
I also finish off my side dots. This was most likely the easiest thing that I have done to date. It may have been harder if I didn't have the drill press but the results are instant and easy to get correct.
Perry Orsmby returned my email. Unfortunately he does not have inlay classes but he has offered to provide a quote as to what it will cost to do it for me. I am a little undecided on this one. Perhaps I should leave them out, after all maybe everything should be done by my hands.
Time taken : 1.5 hours
Tools used : shooting board, craft knife, chisel
AU$'s spent : Nil
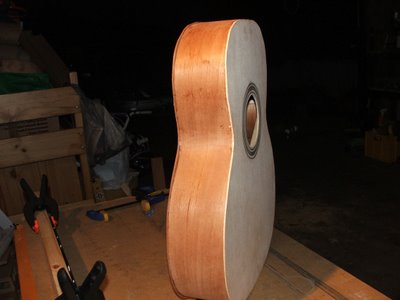
If you look hard, you can see where the kids wrote on the back, but you have to go looking for it.
Tonight I cleared out the top of the soundboard where the neck will attach and then I started to trim down the edges. This job, I suggest you do in phases because I found myself getting cocky with the chisel and really digging in. It would not take too much to drive the chisel right into the sides.
I also finish off my side dots. This was most likely the easiest thing that I have done to date. It may have been harder if I didn't have the drill press but the results are instant and easy to get correct.
Perry Orsmby returned my email. Unfortunately he does not have inlay classes but he has offered to provide a quote as to what it will cost to do it for me. I am a little undecided on this one. Perhaps I should leave them out, after all maybe everything should be done by my hands.
Time taken : 1.5 hours
Tools used : shooting board, craft knife, chisel
AU$'s spent : Nil
Sunday, August 20, 2006
Inlay is not for beginners
Having spent a good part of the afternoon and evening, throwing craft knives, chisels, and the Dremel across the workshop, I have formed the opinion that inlay work is really hard. Why StewMac would put square shaped fret inlays for beginners to put onto a curved fret board, I have no idea. Obviously round dots, the same shape as a drill bit would have been better.
I have come to the conclusion that I do not have the time, skill or equipment to competently (or close to it) inlay these markers. I'd prefer to have no markers than feel a bump or dip each time I move over the 5th fret.
Greg, one of the guys that checks in on me, pointed me towards Perth luthier Perry Ormsby. I see that he has guitar making classes and that he is quite experienced at inlay work. I've emailed Perry, asking if he holds inlay classes. Might be the best way I can learn this particular skill. Alternatively, I will leave out the fret board inlay steps and just try my hand at the headstock. I can live with an imperfect headstock It'll be like a personal touch.
So, I've moved ahead regardless. I finished shooting the fret board. It is close to being exactly the same width as the neck itself.

And lastly I put in the side dots. When did they stop marking the 3rd fret? I did it without thinking, then I looked at my other guitars  apparently I am the only maker that does it.
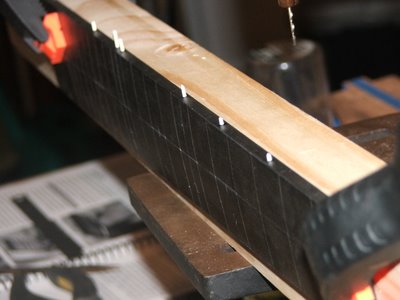
Somewhere in the middle of having inlay brain snaps, special moments with the kids and almost gluing my fingers to the fret board, I must have had a female moment... I cured all my problems with a quick, sharpe burst of rtherapyheropy. I've put my routing worries to rest and bought the StewMac precision router set up and a simple (cheaper) set of tuners... Initially I had planned on the snakewood tuners but, the cost is getting away from me at the moment. I refuse to start adding it up until I have the finished product... but I know it's going to be scary.
Time taken : 2 hours
Tools used : superglue, sandpaper (shooting board), all the inlay stuff (arrrhh), rounded clippers, craft knife, drill press, clamps.
AU$'s spent : $127.79 StewMac Precision Router Set, $40.84 Nickel Grover 18:1 Sta-Tite Slotted Peghead Guitar Machines, $36.82 postage.
I have come to the conclusion that I do not have the time, skill or equipment to competently (or close to it) inlay these markers. I'd prefer to have no markers than feel a bump or dip each time I move over the 5th fret.
Greg, one of the guys that checks in on me, pointed me towards Perth luthier Perry Ormsby. I see that he has guitar making classes and that he is quite experienced at inlay work. I've emailed Perry, asking if he holds inlay classes. Might be the best way I can learn this particular skill. Alternatively, I will leave out the fret board inlay steps and just try my hand at the headstock. I can live with an imperfect headstock It'll be like a personal touch.
So, I've moved ahead regardless. I finished shooting the fret board. It is close to being exactly the same width as the neck itself.

And lastly I put in the side dots. When did they stop marking the 3rd fret? I did it without thinking, then I looked at my other guitars  apparently I am the only maker that does it.
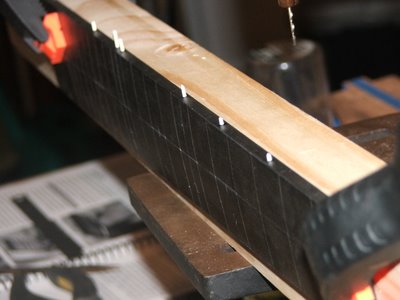
Somewhere in the middle of having inlay brain snaps, special moments with the kids and almost gluing my fingers to the fret board, I must have had a female moment... I cured all my problems with a quick, sharpe burst of rtherapyheropy. I've put my routing worries to rest and bought the StewMac precision router set up and a simple (cheaper) set of tuners... Initially I had planned on the snakewood tuners but, the cost is getting away from me at the moment. I refuse to start adding it up until I have the finished product... but I know it's going to be scary.
Time taken : 2 hours
Tools used : superglue, sandpaper (shooting board), all the inlay stuff (arrrhh), rounded clippers, craft knife, drill press, clamps.
AU$'s spent : $127.79 StewMac Precision Router Set, $40.84 Nickel Grover 18:1 Sta-Tite Slotted Peghead Guitar Machines, $36.82 postage.
CRACK!!! - F*#@ - Oh thank God
Well the back is on... Just.

I was doing a last little bit of adjusting and preparing, whilst I was finger tightening a clamp, I heard this great big cracking sound, a sound that I knew immediately was wood - cracking, and bad.
I swore, closed my eyes and turned my back on the guitar.
When I looked back again - the relief was huge. The waste clamp had snapped. The piece of pine that I used to make it had a knot running through it and this is where the clamp eventually let go. No damage done, just a few years off my life.
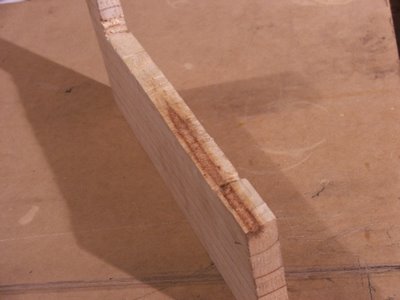
Time taken : 1 hour
Tools used : glue, clamps, scrap pine (new waste clamp) pencil, ruler
AU$'s spent : Nil

I was doing a last little bit of adjusting and preparing, whilst I was finger tightening a clamp, I heard this great big cracking sound, a sound that I knew immediately was wood - cracking, and bad.
I swore, closed my eyes and turned my back on the guitar.
When I looked back again - the relief was huge. The waste clamp had snapped. The piece of pine that I used to make it had a knot running through it and this is where the clamp eventually let go. No damage done, just a few years off my life.
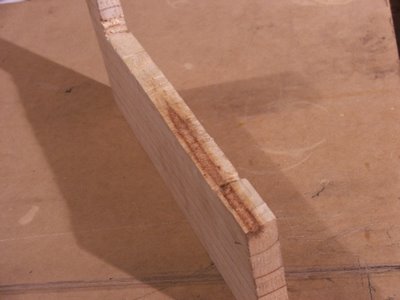
Time taken : 1 hour
Tools used : glue, clamps, scrap pine (new waste clamp) pencil, ruler
AU$'s spent : Nil
A family moment
With all trimming the sides and kerfing done and after a few dry clamping runs, I have reached the point where I will close the box - put the back on. I thought that it would be nice to have my two daughters write on the back. I'll remember it's there a long time after they have grown up - gets back to one of my reasons for making my own guitar in the first place.
Courtney (7 years old) wrote a message like a short biography, mentioning where she was born and when. Brooke (4) simply wrote her name.
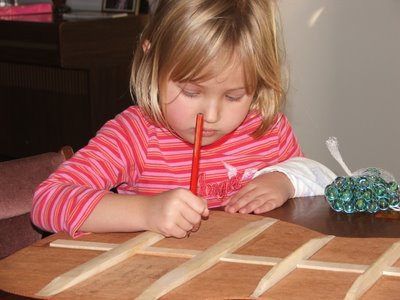
I've also started working at putting the inlay into the fret board. I cut up small squares of the pearl inlay I bought last week and started inlaying it into a piece of pine. I am a little concerned that I will develop a technique that will only suit soft woods. I am back to craft knife, scraping, slowly slowly does it.
Time taken : 2 hours
Tools used : clamps, pencil, craft knife,
AU$'s spent : Nil
Courtney (7 years old) wrote a message like a short biography, mentioning where she was born and when. Brooke (4) simply wrote her name.
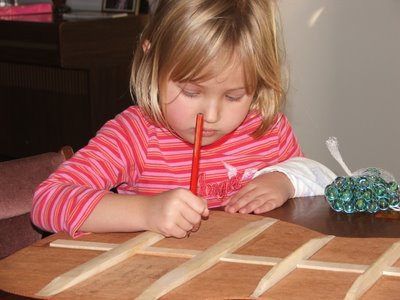
I've also started working at putting the inlay into the fret board. I cut up small squares of the pearl inlay I bought last week and started inlaying it into a piece of pine. I am a little concerned that I will develop a technique that will only suit soft woods. I am back to craft knife, scraping, slowly slowly does it.
Time taken : 2 hours
Tools used : clamps, pencil, craft knife,
AU$'s spent : Nil
Off Topic: Highs and Lows
Firstly, I am now an international superstar and well published author... well sort of. Earl was kind enough to post a mention of tedsguitar on his site, guitarguitarguitar. I have no doubt at all that very soon the name Ted sit proudly beside other authors such as Cumpiano and Netelson.
Scrolling through Earl's site I found so very disturbing news. Olga has been served with a take down notice which in effect removes one of the largest collections of guitar tab and chords going around. Obviously there are other places on the net but, is this just the start?
Now, I can totally understand why the corporate music world went hunting after Napster and other peer to peer music trading sites, but when it comes down to internet quality tab and chords I think they have gone too far. What's next? will they start asking high school bands for royalties each time they play a song. What percentage of an artist's earn is made from the sale of music books.
Another point is that these books are notoriusly bad. They are obviously transcribed by computers at worse, at best a classically trained violinist.
Internet tabs and chords provide the start required for the next generation of guitar players, who will in turn be the next big thing that the music industry will seek a percentage from. Without this resource, kids will have to return to the days rote learning Smoke on the Water, a song from some bad they have never heard off. How many kid will pay $30.00+ to buy a music book?
Time taken : Nil
Tools used : Nil
AU$'s spent : Nil
Scrolling through Earl's site I found so very disturbing news. Olga has been served with a take down notice which in effect removes one of the largest collections of guitar tab and chords going around. Obviously there are other places on the net but, is this just the start?
Now, I can totally understand why the corporate music world went hunting after Napster and other peer to peer music trading sites, but when it comes down to internet quality tab and chords I think they have gone too far. What's next? will they start asking high school bands for royalties each time they play a song. What percentage of an artist's earn is made from the sale of music books.
Another point is that these books are notoriusly bad. They are obviously transcribed by computers at worse, at best a classically trained violinist.
Internet tabs and chords provide the start required for the next generation of guitar players, who will in turn be the next big thing that the music industry will seek a percentage from. Without this resource, kids will have to return to the days rote learning Smoke on the Water, a song from some bad they have never heard off. How many kid will pay $30.00+ to buy a music book?
Time taken : Nil
Tools used : Nil
AU$'s spent : Nil
Saturday, August 19, 2006
More expense
Today I went down to the hardware shop and picked up a Dremel. I've already drawn blood after engraving the end of my finger - great peice of kit. Dad tells me that he will use it all the time so obviously the expense is not wasted on this one project.
It's been one of those days where I've not been able to make a sound start on anything. I cut out the mold this morning and started gluing on the side braces and then I renewed the sand paper on the sanding board.

I marked out the places on my fret board where the snow flake inlays will go and then I started having dry runs at cutting out the squares for the inlay to slot into. I am getting really worried that my skill levels are not high enough to make a decent job out of putting these inlays. Will I be able to get them in neatly without ruining the whole look of the guitar? I hope so. I've gone to the Guitar Builders Forum in an effort to find some ideas as to how to get them in neatly.
The best way I've found so far is to use the Dremel to hollow out the square. I cut the shape required from a piece of masking tape to use as a guide. I can get the piece to fit nicely, just the edges of the square are not sharp. Will this matter? I don't think these inlays are at a beginners level.

Time taken : 2 hours
Tools used : Glue, clamps, pencils, Dremel, drill, craft knife.
AU$'s spent : Dremel $126.00, Clear glue $12.98
It's been one of those days where I've not been able to make a sound start on anything. I cut out the mold this morning and started gluing on the side braces and then I renewed the sand paper on the sanding board.

I marked out the places on my fret board where the snow flake inlays will go and then I started having dry runs at cutting out the squares for the inlay to slot into. I am getting really worried that my skill levels are not high enough to make a decent job out of putting these inlays. Will I be able to get them in neatly without ruining the whole look of the guitar? I hope so. I've gone to the Guitar Builders Forum in an effort to find some ideas as to how to get them in neatly.
The best way I've found so far is to use the Dremel to hollow out the square. I cut the shape required from a piece of masking tape to use as a guide. I can get the piece to fit nicely, just the edges of the square are not sharp. Will this matter? I don't think these inlays are at a beginners level.

Time taken : 2 hours
Tools used : Glue, clamps, pencils, Dremel, drill, craft knife.
AU$'s spent : Dremel $126.00, Clear glue $12.98
Thursday, August 17, 2006
Feeling Good
Rushed home from work today, raced into the shed and starting tearing off those 34 clamps that were holding my soundboard down. I am really happy - It stuck. My greatest fear (second to the routing coming up) has been conquered.
Tonight I glued 80 grit to the 5 degrees side of my sanding board (should have done that days ago) and then I got busy with shooting the fret board. Word to the wise, this takes ages when you don't have a ban saw or similar to get up to the line. I started with the hand plane and then got worried about it tilting to an angle so I went to the board. I have worn grooves into my work top.
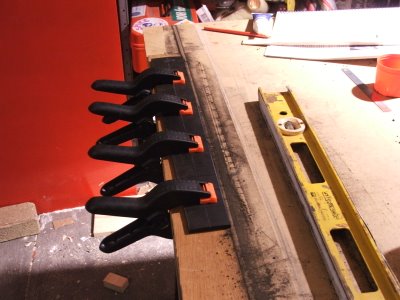
I am a little worried about the taper down to the head. What if I take too much down at the body end... Oh well, I'll just keep edging up to the white line.
Just one point on this - Sanding the fret board makes fine black dust. Your hands get covered in find black dust... Don't put your grubby dirty mitts on your lovely clean soundboard... you'll be upset and start looking forward to sanding off the mess.
Lastly, my inlay arrived today. Looks nice but now I am not so confident and I have no idea what pattern I am going to put in.
Time taken : 2 hours
Tools used : 80 and 120 grit, contact cement, long spirit level, string clamps, craft knife, white pencil, hand plane
AU$'s spent : Nil
Tonight I glued 80 grit to the 5 degrees side of my sanding board (should have done that days ago) and then I got busy with shooting the fret board. Word to the wise, this takes ages when you don't have a ban saw or similar to get up to the line. I started with the hand plane and then got worried about it tilting to an angle so I went to the board. I have worn grooves into my work top.
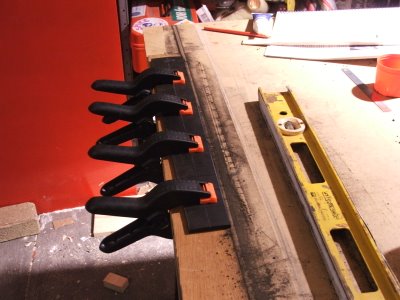
I am a little worried about the taper down to the head. What if I take too much down at the body end... Oh well, I'll just keep edging up to the white line.
Just one point on this - Sanding the fret board makes fine black dust. Your hands get covered in find black dust... Don't put your grubby dirty mitts on your lovely clean soundboard... you'll be upset and start looking forward to sanding off the mess.
Lastly, my inlay arrived today. Looks nice but now I am not so confident and I have no idea what pattern I am going to put in.
Time taken : 2 hours
Tools used : 80 and 120 grit, contact cement, long spirit level, string clamps, craft knife, white pencil, hand plane
AU$'s spent : Nil
Wednesday, August 16, 2006
The Lid Is On !
I have just this minute come inside from gluing on my sound board. It was a little stressful and I was madly zipping around screwing down the bolts on my homemade clamps. I felt there was plenty of glue and in most places I had a decent squeeze out of the glue but in other places none at all - more stress.

It really wasn't that difficult - my greatest concern is that the ends remained square as I forced the bottom up to fit in under the sound board. I guess that it must be - if my measurements are correct - I only had to shift in about 1/8th anyway, so it's not going to be a huge difference.
Recalling this evening - I also signed the sound board and wrote "August 2006 - The First One - Stewart Macdonald OOO" - Stupid me, I signed on the nice flat surface of the bridge plate base, the surface that will soon have 6 holes drilled into it! Mess up number #??? complete.
Time taken : 1 hour
Tools used : glue, clamps, socket set and ring spanner.
AU$'s spent : Nil

It really wasn't that difficult - my greatest concern is that the ends remained square as I forced the bottom up to fit in under the sound board. I guess that it must be - if my measurements are correct - I only had to shift in about 1/8th anyway, so it's not going to be a huge difference.
Recalling this evening - I also signed the sound board and wrote "August 2006 - The First One - Stewart Macdonald OOO" - Stupid me, I signed on the nice flat surface of the bridge plate base, the surface that will soon have 6 holes drilled into it! Mess up number #??? complete.
Time taken : 1 hour
Tools used : glue, clamps, socket set and ring spanner.
AU$'s spent : Nil
Tuesday, August 15, 2006
Another day off?
Again there was no work today (I am all but in strike) so I got to play around with my guitar. It poured down today, cats and dogs kids of weather - an amazing thing last night, I went to glue the last of the centre line braces to my back board. The wood was like a realy firm putty... I could bend it between two fingers... now I understand (or start to) humidity.
Being wet, I am limited as to what I can do, but I have finished the braces.

This morning I built 15 more clamps, just like I did yesterday and then I started making dry runs at getting the sound board onto the edges.

I am amazed at the amount of pressure that this box will be under - no gluing or elsewise today - I have to wait until the humidity settles down. Who would dare glue their box shut in this weather?

Time taken : 3 hours
Tools used : hack saw, drill press, saw table, glue, rulerd
AU$'s spent : $27.00 again
Being wet, I am limited as to what I can do, but I have finished the braces.

This morning I built 15 more clamps, just like I did yesterday and then I started making dry runs at getting the sound board onto the edges.

I am amazed at the amount of pressure that this box will be under - no gluing or elsewise today - I have to wait until the humidity settles down. Who would dare glue their box shut in this weather?

Time taken : 3 hours
Tools used : hack saw, drill press, saw table, glue, rulerd
AU$'s spent : $27.00 again
Monday, August 14, 2006
No work today
No work today, so Ted gets to play.
This morning I headed off to Bunnings again to get supplied to make the spool clamps. A suitable length and size of dowel was going to cost something like $50.00 so I had a little head scratch and came up with an alternative.
I bought two 70 X 30mm X 0.9M pine boards, five 24 X 1/4 inch all threaded steel rod, 30 1/4 inch nuts and 30 washers.
When I got home, I made up the table saw and cut the board into one inch wide blocks, thirty of them. Then I drilled a 1/4 inch hole through each one and using super glue, stuck on a piece of the thick cardboard left over from making the inner mold.
Once all together, I ended up with 15 clamps - Which leaves me 15 clamps short as it turns out. I will but have to duplicate the whole procees again tomorrow before I am able to tackle closing the box.
Not content on having spent enough cash today - I flipped out the old Visa card and bought an once of inlay pearl from Australian Luthier Supplies. Your guess is as good as mine as to what I am going to do with it but my plan is to have a go at making some sort of signature inlay. Crazy thinking maybe.
Time taken : 3 hours
Tools used : hack saw, saw table, drill press, super glue, rulers, pencils
AU$'s spent : Items detailed above $27.11
This morning I headed off to Bunnings again to get supplied to make the spool clamps. A suitable length and size of dowel was going to cost something like $50.00 so I had a little head scratch and came up with an alternative.
I bought two 70 X 30mm X 0.9M pine boards, five 24 X 1/4 inch all threaded steel rod, 30 1/4 inch nuts and 30 washers.
When I got home, I made up the table saw and cut the board into one inch wide blocks, thirty of them. Then I drilled a 1/4 inch hole through each one and using super glue, stuck on a piece of the thick cardboard left over from making the inner mold.
Once all together, I ended up with 15 clamps - Which leaves me 15 clamps short as it turns out. I will but have to duplicate the whole procees again tomorrow before I am able to tackle closing the box.
Not content on having spent enough cash today - I flipped out the old Visa card and bought an once of inlay pearl from Australian Luthier Supplies. Your guess is as good as mine as to what I am going to do with it but my plan is to have a go at making some sort of signature inlay. Crazy thinking maybe.
Time taken : 3 hours
Tools used : hack saw, saw table, drill press, super glue, rulers, pencils
AU$'s spent : Items detailed above $27.11
Sunday, August 13, 2006
Box coming together.
Well I was a little disappointed with the wood show. I guess it would have been okay if you were looking for a piece of machinery but there was no makers of instruments, no stalls dealing with finishes or paints and nothing in relation to inlays or decorations etc. It really didn't suit someone in my position.
I did get a chance to look at the Dremels and a lot of similar tools and a few small routers and trimmers. I think I am going to settle on the Dremel and go ahead and order the precision router kit from StewMac. In relation to routing the I am (again) flipping from one choice to another. It is my latest task that I am worried about, as to whether or not I will be able to complete it properly.
At the wood show, I bought the biggest, flashest and hi tech(est) protractor that I saw. I got it home and then I found out that it did not measure below 15 degrees - great. I had a quick sulk and then got out that old plastic school protractor and made the sanding board, cutting the angel with a jigsaw. After all the thinking and planning, dumbing it down worked fairly well.
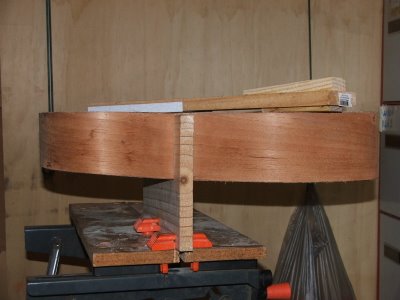
I used contact cement to attach a piece of 80 grit sandpaper to the board and then sanded back the top edge. The sanding seemed to go well however the vibration made a gap between the inner cardboard mold and the edges. I squared the ends up again and there does not appear to be any dramas.
After that I notched out the kerfing where the braces a meant to touch. The top seams to close tightly but I have no idea if the braces are still making contact with the kerfing.
I would have thought for a beginners kit that there would have been more overlay in the soundboard. When I measure 5 3/8" from the top of the sound board the mark is right at the top. There is only 1/8th of an inch allowance at the bottom. Tight.
While I had the jig saw out, I also cut the curve (best I could) for the back braces and I glued the first two into place.
Time taken : 3 hours
Tools used : chisels, jigsaw, handsaw, protractor, sandpaper, contact cement, file, rulers, clamps, glue, black and white pencil, T-square.
AU$'s spent : $19.00 on a protractor I can not use.
I did get a chance to look at the Dremels and a lot of similar tools and a few small routers and trimmers. I think I am going to settle on the Dremel and go ahead and order the precision router kit from StewMac. In relation to routing the I am (again) flipping from one choice to another. It is my latest task that I am worried about, as to whether or not I will be able to complete it properly.
At the wood show, I bought the biggest, flashest and hi tech(est) protractor that I saw. I got it home and then I found out that it did not measure below 15 degrees - great. I had a quick sulk and then got out that old plastic school protractor and made the sanding board, cutting the angel with a jigsaw. After all the thinking and planning, dumbing it down worked fairly well.
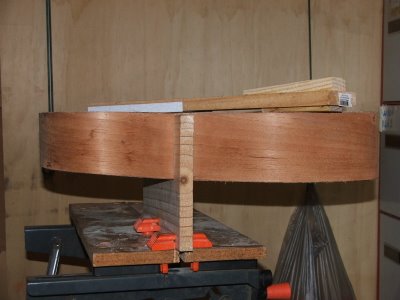
I used contact cement to attach a piece of 80 grit sandpaper to the board and then sanded back the top edge. The sanding seemed to go well however the vibration made a gap between the inner cardboard mold and the edges. I squared the ends up again and there does not appear to be any dramas.
After that I notched out the kerfing where the braces a meant to touch. The top seams to close tightly but I have no idea if the braces are still making contact with the kerfing.
I would have thought for a beginners kit that there would have been more overlay in the soundboard. When I measure 5 3/8" from the top of the sound board the mark is right at the top. There is only 1/8th of an inch allowance at the bottom. Tight.
While I had the jig saw out, I also cut the curve (best I could) for the back braces and I glued the first two into place.
Time taken : 3 hours
Tools used : chisels, jigsaw, handsaw, protractor, sandpaper, contact cement, file, rulers, clamps, glue, black and white pencil, T-square.
AU$'s spent : $19.00 on a protractor I can not use.
Saturday, August 12, 2006
Bits and Pieces
Today has been an odds and ends day. I am starting to get little parts started but I think it’s time that I pulled them all together and got back on track or I am going to start making mistakes.
Today I drew the center lines on my fingerboard and the then marked the edges. I planed up to within 5 mm of the side lines but then lost my nerve and put that away. The trust rod slides into the neck easily and because I am using the bolt on neck, there was no need to drill the hole as mentioned in the instruction manual.
I have chiseled the small braces down to nothing against the soundboard but I have no idea how big .100” is… That’s not on my conversion table so I will have to ask the internet after I finish this post.
I made the shoulder and bridge cauls as well although I think I might do them again. They are snug but not perfect. I might get Dad’s table saw out soon and make better ones.
Today I have learnt that using sharp tools (chisels) makes work neater and more professional in appearance. I will certainly be learning how to sharpen a chisel before I try to shape the diamond on the back of the neck.
I also made a caul for the back braces. Not having a ban saw, I am having a hard time working out how I going the cut the curve. I have tried using the auto body filling putty just as I did with the neck and end blocks. I have only made one so (if it works) it’ll be slow going putting the back together.
I am stuck on how to make the sanding board for the edges. How to make the 5 and 1 ½ degree angles have stumped. I only have my old high school protractor and I am not really confident that the measurements will be correct.
Tomorrow, Dad and I are going to the annual wood show, so I’ll get the chance to see lots of goodies and I might get a chance to start thinking about finishes.
Another opportunity to spend money. I did fairly well at Bunnings today, buying supplies I think I will need in the near future.
Time taken : 2 hours
Tools used : chisel, clamps, hand saw, sand paper, auto putty, hand plane, white pencil,
U$'s spent : Curves cutters (Fret snips) $14.95, wire brush $1.45, Soft faced hammer $14.85, masking tape $12.90, gaffa tape $6.40, Contact cement $6.20, sand paper $6.00
Today I drew the center lines on my fingerboard and the then marked the edges. I planed up to within 5 mm of the side lines but then lost my nerve and put that away. The trust rod slides into the neck easily and because I am using the bolt on neck, there was no need to drill the hole as mentioned in the instruction manual.
I have chiseled the small braces down to nothing against the soundboard but I have no idea how big .100” is… That’s not on my conversion table so I will have to ask the internet after I finish this post.
I made the shoulder and bridge cauls as well although I think I might do them again. They are snug but not perfect. I might get Dad’s table saw out soon and make better ones.
Today I have learnt that using sharp tools (chisels) makes work neater and more professional in appearance. I will certainly be learning how to sharpen a chisel before I try to shape the diamond on the back of the neck.
I also made a caul for the back braces. Not having a ban saw, I am having a hard time working out how I going the cut the curve. I have tried using the auto body filling putty just as I did with the neck and end blocks. I have only made one so (if it works) it’ll be slow going putting the back together.
I am stuck on how to make the sanding board for the edges. How to make the 5 and 1 ½ degree angles have stumped. I only have my old high school protractor and I am not really confident that the measurements will be correct.
Tomorrow, Dad and I are going to the annual wood show, so I’ll get the chance to see lots of goodies and I might get a chance to start thinking about finishes.
Another opportunity to spend money. I did fairly well at Bunnings today, buying supplies I think I will need in the near future.
Time taken : 2 hours
Tools used : chisel, clamps, hand saw, sand paper, auto putty, hand plane, white pencil,
U$'s spent : Curves cutters (Fret snips) $14.95, wire brush $1.45, Soft faced hammer $14.85, masking tape $12.90, gaffa tape $6.40, Contact cement $6.20, sand paper $6.00
Thursday, August 10, 2006
Top braces on
Today the last of the braces for the top went on and they are now ready for shaping. The soundboard has certainly gained weight - a lot heavier than I expected. Although I've got nothing to compare it with, I am happy with the result.

While the last of the braces were in clamps I trimed the headstock overlay, drill out the centres and filed and sanded the basic shape. Obviously I need more sanding and I have to work out how much room the strings need, but it's coming along okay. I found that it was easiest to form the shape by wrapping a sheet of sand paper around a thick texta. The round shape sanding surface made it easier to form the shape required.

Time to start slowing down I think. Perhaps I am getting a bit of confidence but I feel like I am going too fast and backing myself too much. Tonight I dragged the file right across the top of the head stock overlay. I've got no doubt that it'll sand out very quickly but still, I'm getting to the stage where my mistakes will show up - they won't be inside the box.
Time taken : 2 hours
Tools used : Glue, rags, clamps, craft knife, file, sand paper and texta.
AU$'s spent : Nil

While the last of the braces were in clamps I trimed the headstock overlay, drill out the centres and filed and sanded the basic shape. Obviously I need more sanding and I have to work out how much room the strings need, but it's coming along okay. I found that it was easiest to form the shape by wrapping a sheet of sand paper around a thick texta. The round shape sanding surface made it easier to form the shape required.

Time to start slowing down I think. Perhaps I am getting a bit of confidence but I feel like I am going too fast and backing myself too much. Tonight I dragged the file right across the top of the head stock overlay. I've got no doubt that it'll sand out very quickly but still, I'm getting to the stage where my mistakes will show up - they won't be inside the box.
Time taken : 2 hours
Tools used : Glue, rags, clamps, craft knife, file, sand paper and texta.
AU$'s spent : Nil
Wednesday, August 09, 2006
Braces and Headstock
I’ve continued with gluing the braces to the soundboard and it seems like everything is going along as planned. Obviously my progress is limited by the number of clamps that I have available and the amount of surface area on which to place those clamps.
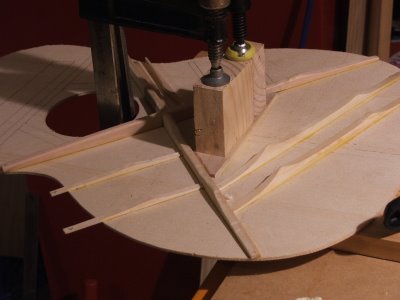
Tonight I made a brief start on my neck, or should I say the headstock. I glued the overlay onto the headstock. I have a little concern over the glue squeeze out on the inside of the headstock, it was only once the cauls were in place that I thought about it. If I was to do it again, I’d consider packing the inside of the head with some paper or something to absorb most of the glue.


Time taken : 2 hours
Tools used : glue, clamps, scrap wood, tape, cardboard, ruler, rags
AU$'s spent : Nil
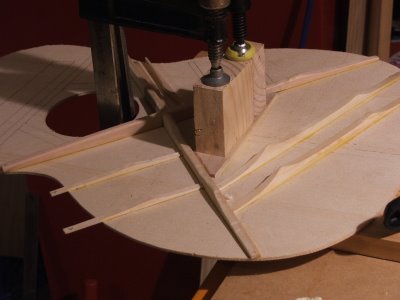
Tonight I made a brief start on my neck, or should I say the headstock. I glued the overlay onto the headstock. I have a little concern over the glue squeeze out on the inside of the headstock, it was only once the cauls were in place that I thought about it. If I was to do it again, I’d consider packing the inside of the head with some paper or something to absorb most of the glue.


Time taken : 2 hours
Tools used : glue, clamps, scrap wood, tape, cardboard, ruler, rags
AU$'s spent : Nil
Tuesday, August 08, 2006
It's just like golf

I have worked out that this guitar making business is like golf. I used to play a little and I remember that you would spend hours and hours slicing and hooking all over the place and then you'd get that one good shot. The perfect drive or the 15 foot putt. That shot would convince you that you were capable of playing like a pro and get you back next week.
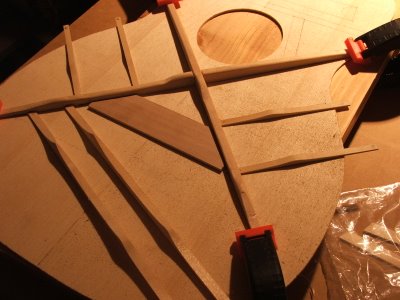
Tonight I made the second set of cross braces, shaped them and then slotted the reliefs for the other braces and bridge plate. I am on fire. It all felt good and I really enjoyed my time tonight. Now I am not saying that it is perfect - but it's mine. After last nights last minute dash to have the old braces taken off I felt like I was going in the right direction again.

Time taken : 3.5 hours
Tools used : sandpaper, coping saw, Japanese saw, spring and normal clamps, craft knife, pencil, ruler, T Square, rags.
AU$'s spent : Nil
Monday, August 07, 2006
I make mistakes for you all to learn
Well at least that is my story and I am sticking to it.
A couple of posts ago I mentioned that I had a couple of pieces of wood that had "Glue this side" written on them. I scratched my head, laid everything out on the paper, watched the video and even read the manual - it just did not sink in.
I had formed the impression that the manual for the dreadnought kit doubled as the OOO manual as the dovetail does for the bolt on. Wrong.
So after I worked out, this brace goes there, this one goes there - they look just like the picture in the book and on the video I had come to the conclusion that these two bits of wood were mistakenly packed or something... There was enough pieces in the top brace kit, I didn't need anymore.
Thank goodness that I speared in an email to StewMac asking the question. Tonight - AFTER - I had glued the dreadnought cross braces to my OOO soundboard with great detail. Erick replied to my email, letting me know that the bits of wood were the OOO braces to be substituted for the dreadnought braces.
I go back now and read the instruction manual again and it all appears so clear. I must have had a brain fizz and switched off when I saw the word Dreadnought - I must have missed the whole paragraph.
I feel stupid and a little unnerved but the glue had not gone off totally - I managed to get the braces up without doing damage to the top. At least I've answered my earlier question about how much pressure I need to settle the cross brace. Another couple of hours and those incorrect braces would never have come up.
Note for those that follow : There are an extra set of braces added to the OOO kit. Do not use the ones in the package.
At least now I get another chance at making those reliefs into the cross braces. It's all good.
Time taken : 15 minutes (to remove the braces)
Tools used : Hair dryer, very thin paint scraper
AU$'s spent : Nil - but it could have been worse.
A couple of posts ago I mentioned that I had a couple of pieces of wood that had "Glue this side" written on them. I scratched my head, laid everything out on the paper, watched the video and even read the manual - it just did not sink in.
I had formed the impression that the manual for the dreadnought kit doubled as the OOO manual as the dovetail does for the bolt on. Wrong.
So after I worked out, this brace goes there, this one goes there - they look just like the picture in the book and on the video I had come to the conclusion that these two bits of wood were mistakenly packed or something... There was enough pieces in the top brace kit, I didn't need anymore.
Thank goodness that I speared in an email to StewMac asking the question. Tonight - AFTER - I had glued the dreadnought cross braces to my OOO soundboard with great detail. Erick replied to my email, letting me know that the bits of wood were the OOO braces to be substituted for the dreadnought braces.
I go back now and read the instruction manual again and it all appears so clear. I must have had a brain fizz and switched off when I saw the word Dreadnought - I must have missed the whole paragraph.
I feel stupid and a little unnerved but the glue had not gone off totally - I managed to get the braces up without doing damage to the top. At least I've answered my earlier question about how much pressure I need to settle the cross brace. Another couple of hours and those incorrect braces would never have come up.
Note for those that follow : There are an extra set of braces added to the OOO kit. Do not use the ones in the package.
At least now I get another chance at making those reliefs into the cross braces. It's all good.
Time taken : 15 minutes (to remove the braces)
Tools used : Hair dryer, very thin paint scraper
AU$'s spent : Nil - but it could have been worse.
What am I doing?
It occurred to me this evening that I have no idea whatsoever as to what I am doing. It was as something as simple as putting the clamps onto the cross brace that I was reminded that I am not a master craftsman. How tight to you put the clamps on? The soundboard is such a thin piece of wood that if as soon as you put pressure on to the clamps, it bends. How much pressure does the glue need to form a sound bond? How much down force do those Gobar desks put on the braces... should I have used once of those?
Even the weight of the clamps has caused the soundboard to form a shape. I just don't know if the change in shape is a permanent fixture or not.
Still it can't be all my fault, I've notice that ever since I have put the rosette in place, the soundboard has curved slightly. I just hope that when all is said and done, the sides will force the top, the top will pursueded the back..etc and everything will be fine .
Time taken : 1 hour
Tools used : glue, 4 spring clamps, 4 clamps, cardboard/scrap wood etc for cauls
AU$'s spent : Nil
Even the weight of the clamps has caused the soundboard to form a shape. I just don't know if the change in shape is a permanent fixture or not.
Still it can't be all my fault, I've notice that ever since I have put the rosette in place, the soundboard has curved slightly. I just hope that when all is said and done, the sides will force the top, the top will pursueded the back..etc and everything will be fine .
Time taken : 1 hour
Tools used : glue, 4 spring clamps, 4 clamps, cardboard/scrap wood etc for cauls
AU$'s spent : Nil
Sunday, August 06, 2006
Glue this side?
Well, the last of the kerfing is in place. The patch up is not pretty but it is firm and I think it'll do the job. Gluing the kerfing on was really an easy step. I spread the glue the whole length of the kerfing and then put a peg right at the end, this way the kerfing was held up of the cardboard mold while I set the rest in place.

It looks a hole heap better when you don't know exactly where the mistakes are.

Tonight I started putting the top braces together. I was on fire for a little while and then my hands remembered that I am not very experienced at working with wood. The join that I made in the two cross braces was perfect, most of it was done with sandpaper on a board that was right thickness. Then I started making the the reliefs into the cross braces - these are not pretty.

In other news, I am a little confused. I sorted out the issue that StewMac have an error in their manual where they list the items that should be in the kit. The photos for the top and back braces are around the wrong way and they don't tell you that you have to cut one of the braces, to make the three pieces around the sound hole.
The one I can not work out in why I have two curved braces that have "glue this side" written on them in red ink. I've sent StewMac and email asking for clarification - I'm not starting to glue the braces until I find out what they are.
Time taken : 2.5 hours
Tools used : glue, pegs, ruler, pencil, spring clamps, Japanese saw, chisel, craft knife, sand paper, wood files.
AU$'s spent : Nil

It looks a hole heap better when you don't know exactly where the mistakes are.

Tonight I started putting the top braces together. I was on fire for a little while and then my hands remembered that I am not very experienced at working with wood. The join that I made in the two cross braces was perfect, most of it was done with sandpaper on a board that was right thickness. Then I started making the the reliefs into the cross braces - these are not pretty.

In other news, I am a little confused. I sorted out the issue that StewMac have an error in their manual where they list the items that should be in the kit. The photos for the top and back braces are around the wrong way and they don't tell you that you have to cut one of the braces, to make the three pieces around the sound hole.
The one I can not work out in why I have two curved braces that have "glue this side" written on them in red ink. I've sent StewMac and email asking for clarification - I'm not starting to glue the braces until I find out what they are.
Time taken : 2.5 hours
Tools used : glue, pegs, ruler, pencil, spring clamps, Japanese saw, chisel, craft knife, sand paper, wood files.
AU$'s spent : Nil
Note to self
When you clamp the rosette between two boards overnight. Don't forget the wax paper.
Time taken : Nil
Tools used : Obviously not a brain
AU$'s spent : Nil
Time taken : Nil
Tools used : Obviously not a brain
AU$'s spent : Nil
Saturday, August 05, 2006
Moving right along
It has been a fairly productive evening. I went to the shops and picked up a packet of pegs. Believe it or not, I could not find wood pegs anywhere so I had to settle for plastic ones - they appear to have fairly strong spring so they should do the job.
I learnt a valuable lesson tonight, a mistake I don't intend to repeat. Everywhere you read, people tell you to practice clamping before you glue. I found out tonight that this does not apply to kerfing. I had a couple of dry runs and worked out that it is better to start at the tail, otherwise the place where the next strip starts in in the waist. It appears easier to start at either block and work towards the middle. Anyway, bending the kerfing and moving it around obviously made it weak because is snapped. I have a 2-3 inch gap that needs to be patched up.
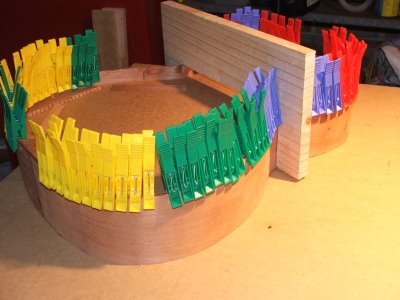
I also installed the rosette. This is the first time where I started to see how this instrument is going to be full of little tell tale signs that it was made by me, good or bad. I made the joins in the rosette as neat as I could however they appear quite messy close up.

From a distance I you might not be able to notice

The rosette was so tight. I don't think I actually needed to glue it in there. I am sure it won't be coming out in a hurry.
Time taken : 1.5 hours
Tools used : 92 plastic pegs, glue, Japanese saw, ruler, chisel
AU$'s spent : $12.00 for the pegs
I learnt a valuable lesson tonight, a mistake I don't intend to repeat. Everywhere you read, people tell you to practice clamping before you glue. I found out tonight that this does not apply to kerfing. I had a couple of dry runs and worked out that it is better to start at the tail, otherwise the place where the next strip starts in in the waist. It appears easier to start at either block and work towards the middle. Anyway, bending the kerfing and moving it around obviously made it weak because is snapped. I have a 2-3 inch gap that needs to be patched up.
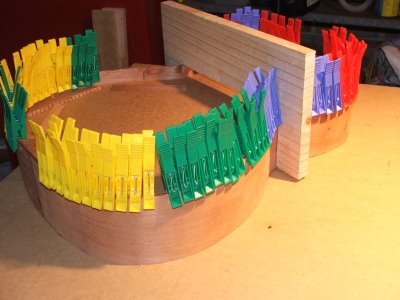
I also installed the rosette. This is the first time where I started to see how this instrument is going to be full of little tell tale signs that it was made by me, good or bad. I made the joins in the rosette as neat as I could however they appear quite messy close up.

From a distance I you might not be able to notice

The rosette was so tight. I don't think I actually needed to glue it in there. I am sure it won't be coming out in a hurry.
Time taken : 1.5 hours
Tools used : 92 plastic pegs, glue, Japanese saw, ruler, chisel
AU$'s spent : $12.00 for the pegs
Thursday, August 03, 2006
The mold is on
After dinner I cut the cardboard required to make the mold and then headed down to the shed, cut some blocks of wood and then started putting the mold together.
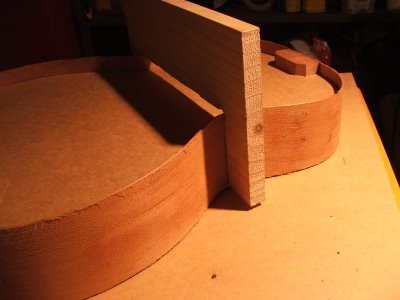
I had been dreading pushing the waist clamp over the sides for a while. As it ended, I felt that it was too tight the first time and then I too a few minutes to file and sand back. The next time, the waist slid firmly over the sides - it felt right.
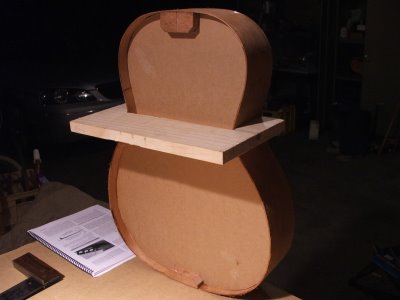
The sides do not exactly follow the cardboard sides but when I messure the length and widths from the plan to my actual shape, they are fairly close so I am happy.
I know I really haven't done anything to date - but it's impressive to stand back and think - that's starting to look like a guitar.
Time taken : 1 hour
Tools used : Stanley trimmer/craft knife, hand saw, wood, super glue, sand paper, wood file
AU$'s spent : Nil
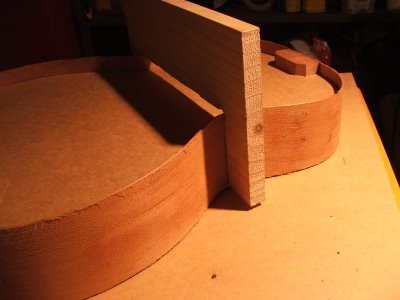
I had been dreading pushing the waist clamp over the sides for a while. As it ended, I felt that it was too tight the first time and then I too a few minutes to file and sand back. The next time, the waist slid firmly over the sides - it felt right.
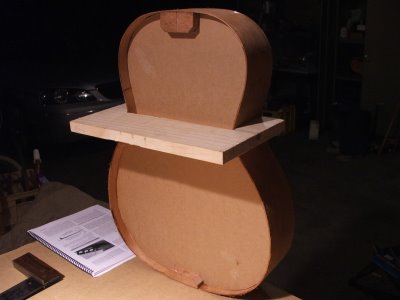
The sides do not exactly follow the cardboard sides but when I messure the length and widths from the plan to my actual shape, they are fairly close so I am happy.
I know I really haven't done anything to date - but it's impressive to stand back and think - that's starting to look like a guitar.
Time taken : 1 hour
Tools used : Stanley trimmer/craft knife, hand saw, wood, super glue, sand paper, wood file
AU$'s spent : Nil
Bugger...
I'm not sure how big a hurdle this is going to cause. Today, I took all the clamps off and found that somehow I must have let the ends slip apart from each other before I clamped them. I am left with a gap between the ends at the neck end. I am not really sure if this is going to cause me that much drama as this area of wood is going to be cut away in order to install the neck. The join appears solid but I wonder if this small error with cause problems with the sides being twisted slightly.

From what I can tell, I may be able to get away with this mistake. I'll throw it open to the forum and see what my brains trust have to offer.
On the flip side of the coin, I am happy with the join at the end.

I think I will put the frame together and await my answer - Hopefully the majority say that I'll be okay.
Time taken : Nil
Tools used : Nil
AU$'s spent : Nil

From what I can tell, I may be able to get away with this mistake. I'll throw it open to the forum and see what my brains trust have to offer.
On the flip side of the coin, I am happy with the join at the end.

I think I will put the frame together and await my answer - Hopefully the majority say that I'll be okay.
Time taken : Nil
Tools used : Nil
AU$'s spent : Nil
Wednesday, August 02, 2006
The sides are on
Today I had the luxury of starting work late and being such a nice day, I decided to get inside the shed and get going with the glue. I found it was a lot easier to adjust the sides once the weighted board was in place across the middle.
I had a few dry runs at each end and then started with the glue. All got very slippery when you add wax paper and glue but I think that it went together quite well.

My only concern is there is a small amount of light now coming through under one of the edges, as in the edge has twisted slightly. I don't think I have a huge need to be worried, as best I can tell the edges are lined up with the centre lines. I am working on the theory that all will come back into alignment once the top, back and braced go on. Time will tell.
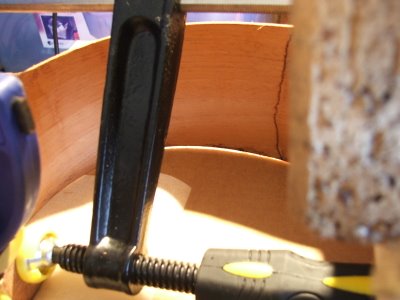
Time taken : An hour
Tools used : 6 clamps, glue, wax paper,
AU$'s spent : Nil
I had a few dry runs at each end and then started with the glue. All got very slippery when you add wax paper and glue but I think that it went together quite well.

My only concern is there is a small amount of light now coming through under one of the edges, as in the edge has twisted slightly. I don't think I have a huge need to be worried, as best I can tell the edges are lined up with the centre lines. I am working on the theory that all will come back into alignment once the top, back and braced go on. Time will tell.
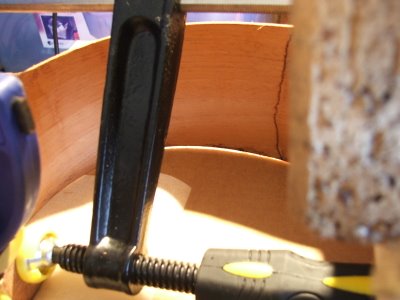
Time taken : An hour
Tools used : 6 clamps, glue, wax paper,
AU$'s spent : Nil
Tuesday, August 01, 2006
Construction of braces
When I sanded back the auto putty it went to a point where the toe of the caul was back to bare wood so I just made up new putty and made a new curve, using the end caul.
After that, I got busy making the U shaped brace for the sides once I glue the ends up. I made it smaller than the template size, just slightly and I with an I also had a few dry runs at gluing the ends up. It is a lot harder to do than it looks on the video. I am starting to worry that I will muck up the simplest of tasks.
I might be getting a bit ahead of myself but I wanted to keep going so I pulled out the top and back to start tracing the outline of the braces. I seemed at first that the top was not long enough, the outline on the template barely fit onto the wood supplied. I used a lawyers bobkin to pierce a hole in the template. In hindsight I might have punched the holes through in the opposite direction first, that way I am not pushing hard onto the wood.

My mistake for today - the dotted lines on the StewMac template - are for the back... there is no need to trace them onto the top...
Time taken : 2 Hours
Tools used : Auto putty, scrap wood, pencil, lawyers bobkin, pencil sharpener, a long ruler, vice, electric drill, hand saw
AU$'s spent : Nil
After that, I got busy making the U shaped brace for the sides once I glue the ends up. I made it smaller than the template size, just slightly and I with an I also had a few dry runs at gluing the ends up. It is a lot harder to do than it looks on the video. I am starting to worry that I will muck up the simplest of tasks.
I might be getting a bit ahead of myself but I wanted to keep going so I pulled out the top and back to start tracing the outline of the braces. I seemed at first that the top was not long enough, the outline on the template barely fit onto the wood supplied. I used a lawyers bobkin to pierce a hole in the template. In hindsight I might have punched the holes through in the opposite direction first, that way I am not pushing hard onto the wood.

My mistake for today - the dotted lines on the StewMac template - are for the back... there is no need to trace them onto the top...
Time taken : 2 Hours
Tools used : Auto putty, scrap wood, pencil, lawyers bobkin, pencil sharpener, a long ruler, vice, electric drill, hand saw
AU$'s spent : Nil
Subscribe to:
Posts (Atom)